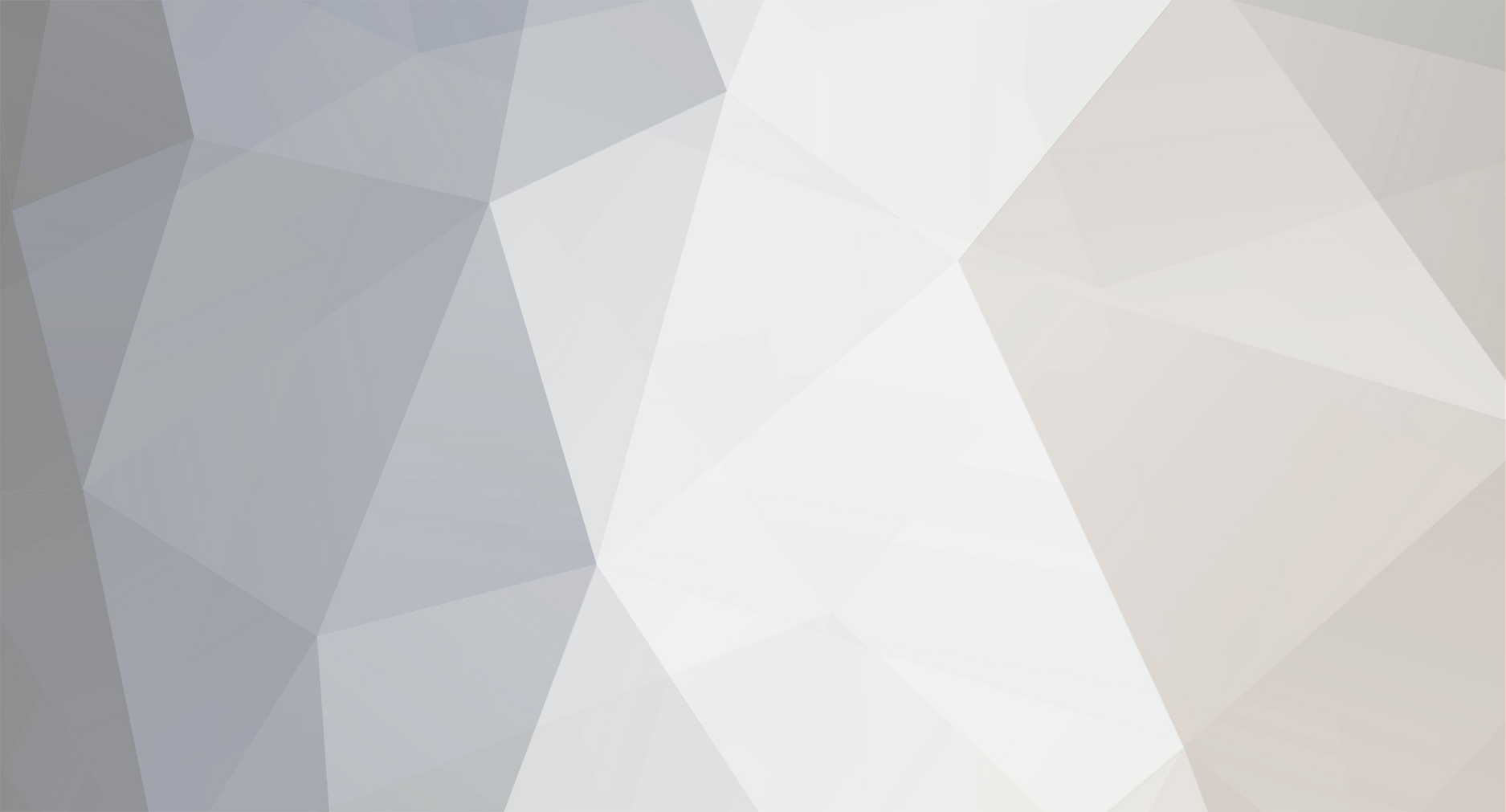
JasonO
-
Posts
99 -
Joined
-
Last visited
-
Feedback
0%
Content Type
Profiles
Forums
Events
Gallery
Media Demo
Store
Posts posted by JasonO
-
-
You're going to try and improve this.......That's a big order
Good luck Christian, I look forward to the results.
-
Correct, which is why I said......Ok, lets start with a few tihngs...1. if you do the rope idea you'll screw the bearings in the alternator or you'll bugger the seal in the water pump.
Kinda like this, but don't use the alternator, put it around the water pump housing so not to damage anything. -
Use the rope trick I mentioned above, exxcept wind the rope the other way around the crank pulley.
-
discopotato,
It's common to run twin 3037's on the Rb26 for 800hp applications, so I think a single would be a bit breathless.
Steve,
Finished the engine build, and it's incredibly strong, pulls from way low down and is much more driveable than it ever was. It's got a really relaxing delivery, with a stupidly wide power band.
But then I took it back off the road, to fit larger injectors, a proper fuel system, and practically all of the Earls hose and fittings catalogue. It's got the 'show' and all it needs now is a proper tuning session to complete the 'go'.
I'll post details when it's all together, shouldn't be much longer now.
-
Steve,
You say you did 10k km's on that turbo, what you running now ?
-
Oh, Just to ad some confusion.......
When I say add duty cycle, it may be that your particular setup needs to remove duty cycle.
You'll get the idea though, and you can work it out by inputing a maximum (90% ?) duty cycle, then a minimum (20% ?)duty cycle and doing the power run thing. One of them will over boost like mad, the other won't reach the target boost.
Sorry, but it is after 6am and I'm kinda tired
-
-
Set them up as you like, my personal preferance is to set 1&2, to my preferred low boost setting, and 3&4 high.
Then I set 1&3 with very conservative duty cycles and 2&4 with aggresive duty cycles.
This gives me plenty of choices.......
1 = Progressive (smooth) low boost, for poor weather, normal running.
2 = Agressive (On/Off) low boost, for good weather, normal running.
3 = Progressive high boost, for poor weather, spirited running.
4 = Agressive high boost, for good weather, spirited running.
The best way to determine the correct duty cycle is through experimentation.
Set the desired boost level, and a mid range duty cycle, then do a power run.
Check to see if you made the target boost.
If not add more duty cycle.
If yes remove duty cycle.
Do another power run to confirm.
When the duty cycle is about correct, you will make the desired boost level, with minimal over spiking.
When you have determined the minimal duty cycle for your desired boost level, this will be your Progressive setting.
Adjusting the duty cycle beyond this minimal point will bring boost on quicker, but with some spiking, a few percent more can make a big difference here and this is where the learning value comes into it's own. When boost spikes over the desired level, the learning value is adjusted, and after some time driving on this setting the ECU will learn to boost quickly with minmal spiking.
-
APEXi describe the value your after as a 'Learning Value', and it's normal to see it change as the boost controller adjusts it's own parameters to fine tune the solenoid.
If the duty cycle is accurately set, then the learning value should change a litle over time, maybe to about 200. If the duty cycle is way off the mark, then the learning value will either be way low, say less than 50, or not reduce at all. In which case you could make some adjustment to the duty cycle to have better boost control.
-
Difficualt to say, as I made so many other changes at the same time, concensus is that there are better ways to spend your money.did it help?
Yep, took quite a bit of work, though nothing too technical.did u put it in urself?
Not hard, just time consuming and involves lots little modifications of different parts of the engine / engine bay.was it hard etcBiggest problem is getting the old plenum off, as it's a pain in the knuckles splitting the OEM plenum from the runners, and there are loads of bolts holding it to the cylinder head, and a multitude of pipes connecting the under side of it that you can't see.
Then you need to build up the GReddy plenum with parts removed form the OEM plenum, and make a few modifications to the wirirng loom that the otherwise good GReddy instructions forgot to mention.
And don't forget to add the cost of the inlet manifold gasket, loads of rubber hose, and the custom IC pipe work.
-
Lukevl,
If it weren't for this continued bickering shite, we may have had an answer to the question by now. :upurs:
Bugger this, I'm going back to my home forum, at least the bickering isn't personal over there :run:
SK,
I'd still like to discuss this even though it's purely academical on my part, as you know I've already made my choice of plenum. You're welcome on the register anytime dude
-
So, Lets get hypothetical then......
I've got an RB25DET, which has had a numerous modifications made to bring it up to the theoretical (mythical) 450bhp limit of the stock plenum, and I just happen to have at my disposal, an RB26 plenum, and a GReddy one.
What do you see as the pros and cons of each in big power the RB25 application ?
-
Bloomin'eck, I hope that's not directed at me, I particularly respect SK's opinion, and have sought him out in the past as a mentor............*mod hat on* Keep it clean guys... *mod hat off*SK,I don't doubt for a second that the GReddy Plenum, in either RB25 or RB26 applications, only comes into it's own after a certain level of airflow is required, nor do I doubt that the OEM designs are good ones, but I'd still love to see the figures so as to appreciate just how futile the whole argument really is.
Like BBQ though, I'd like to know your POV regards the RB26 plenum on an RB25.......
So SK, whadaya reckon ?
-
SK,
I don't doubt for a second that the GReddy Plenum, in either RB25 or RB26 applications, only comes into it's own after a certain level of airflow is required, nor do I doubt that the OEM designs are good ones, but I'd still love to see the figures so as to appreciate just how futile the whole argument really is.
Like BBQ though, I'd like to know your POV regards the RB26 plenum on an RB25.......
-
Don't be dumb !!Agree with discoepotato. Very good statement about Nissan. So true as well. A lot of people think that aftermarket stuff is the be-all and end-all of car developement. None of these guys would have any idea what its like behind the doors of an OEM facility.When Nissan were developing the GTR plenum, they had the same restrictions as they have with everything else they look into when developing a car......Accountants not being the least of their problems, they have to optimise design parameters to suit broad conditions of use. An aftermarket developer, like GReddy, doesn't have to comply with emissions design criteria, and their targeted performance parameters are a heck of a lot narrower than Nissan's ever were.
It's common knowledge that the GTR plenum has a flow problems with Nº1 & 6 cylinders, but I'd love to see evidence of the flow test results you claim to have heard.
-
Lithium,
That sounds like a hoot of a laugh, I must try that sometime
-
The horn is usually mounted on the bar that goes from the slam panel to the lower front chassis crossmember, just below where the bonnet catch plate is and in front of the radiator.
-
:Oops: @ SK,
Sorry dude, thought you were slipping up
-
SK,
Am I that boring
ylwgtr2,
Thanks, good info that, although I would suggest using some nylon or perspex rod rather than a bolt in the plug to avoid any damage to the piston. I have recently rebuilt my engine, and when putting it together, I checked that TDC was accurately marked.
-
SK, You ignoring me, or have I found one you can't answer
Incidentally, The soution to the ignition timing problem required some lateral thinking.
The PFC only shows what it's own IGN Map timing is, it has no way of knowing what the actual timing is as set ont he crank pulley. So, assuming eveything is correctly setup the way forward is to adjust the static timing to match that which is displayed on the PFC. This way what the PFC outputs is relevant to the actual timing on the engine.
So, to answer my original question for future referance.......
The CAS should be adjusted so that the static timing as measured against the crank pulley (harmonic balancer) matches that displayed on the PFC, at idle.
-
SK, I've sked before elsewhere about the engine temp, maybe you can answer this one.
The PFC has a Water Temp Correction, Cranking Time Correction, and several other corrections applied below 80ºC which is the normal running temp.
Will my engines lower running temp bring these into play, or can I disregard them as the temperature difference is minimal ?
-
Sorry not an N1 thermostat, but a NISMO low temp thermostat, IIRC it opens at 62ºC rather than 76.5ºC that the stock thermostat opens.
-
Oi, I try to be accurateI have yet to find an accurate retard on a timing lightHmmm Intresting........I can't get my engine temp over 70 degrees at idle.
I have an N1 water pump and thermostat fitted, and it idles at about 68-70º, only ever gets over 80 degrees at the end of the 1/4, or after a sustained high speed run.
-
The cam gears are spot on, I checked them several times at assembly, and have them checked again since. Everything lines up as it should.
The only problem I have is the PFC doesn't agree with the timing light......
Top Gear Speeds in R33 GTST
in Forced Induction Performance
Posted
The stock engine does have enough grunt to pull top rpm in factory trim.
Looks to me like htere are different gear ratios going around between these cars, which ties in with a converstion I was having this weekend.
4th tops out at 120mph / 7000rpm for me, others I know of get at least another 10mph on top of that.