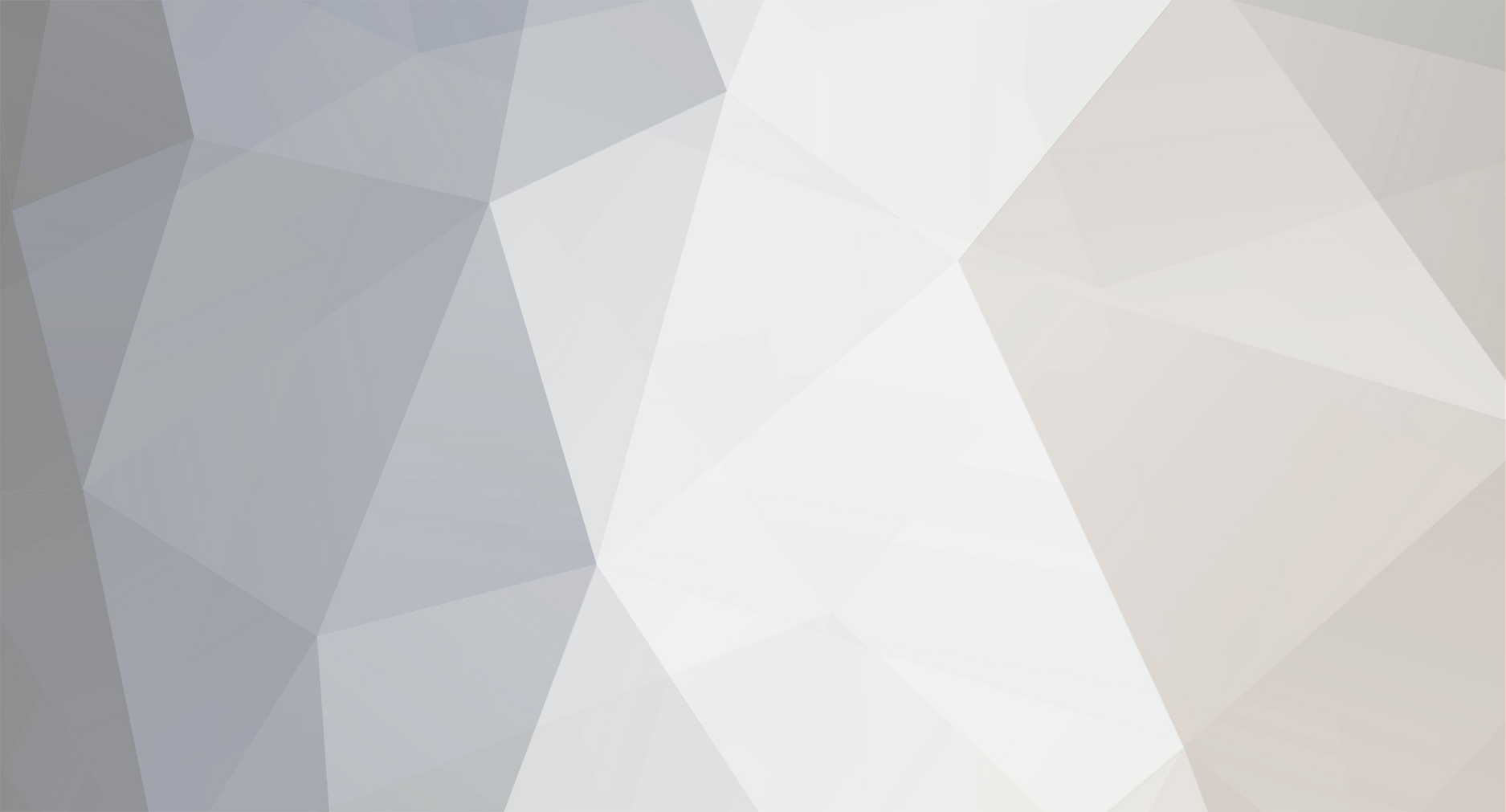
Kevin Johnson
Members-
Posts
13 -
Joined
-
Last visited
-
Feedback
0%
Profile Fields
-
Real Name
Kevin Johnson
Recent Profile Visitors
Kevin Johnson's Achievements
-
Oil Control In Rb's For Circuit Drag Or Drift
Kevin Johnson replied to Sydneykid's topic in Forced Induction Performance
I suggest you read a few of the SAE papers before commenting about how and why restrictors are used for head oil supplies. I have been subscribed to this thread for many years now. I spent a lot of time making thousands upon thousands of posts in other forums dealing with this general topic. I will be quiet now. -
Oil Control In Rb's For Circuit Drag Or Drift
Kevin Johnson replied to Sydneykid's topic in Forced Induction Performance
The titular page shown here is a good start for budding engineers. The investigated engine was also the subject of two MIT theses and subsequent SAE articles. I purposely do not give the links or further information because it is extremely important that people be trained to do research rather than be served pablum. Suffice it to say that the MIT theses can be downloaded and read in their entirety at no charge to the investigator. The SAE articles are not duplicates of the theses, by the way, but do draw upon the research. Just to whet your intellectual curiosity, the engine was originally designed by Porsche. You can learn a lot about engineering by comparing how Ford and Porsche treated sump design differently. Good luck in your investigations. -
Oil Control In Rb's For Circuit Drag Or Drift
Kevin Johnson replied to Sydneykid's topic in Forced Induction Performance
I have examined the sump design on hundreds of different engines including numerous Datsun/Nissan engines. It is very clear that a large effort went into the sump design of the RB26DETT. My criticism would be the corporately dictated bulge in the rear sump floor that disrupts the flow as it does in other Nissan sumps. The engineers have to make the best of that. As far as SAE papers go, there are MANY that deal with air entrainment in oil supplies. I scarcely think that Nissan engineers are ignorant of basic fluid mechanics. SAE.org is your starting point. SAE now provides several pages of the article for viewing prior to purchase. -
Oil Control In Rb's For Circuit Drag Or Drift
Kevin Johnson replied to Sydneykid's topic in Forced Induction Performance
https://physics.stackexchange.com/questions/224523/why-does-the-pressure-of-fluid-increase-when-the-diameter-of-the-pipe-increases If you have entrained or dissolved air bubbles in the oil supply then the marginally larger diameter will help keep the bubbles smaller and/or dissolved. This allows the fluid to act more closely to an ideal fluid which is what the factory engineers envisioned whilst designing the engine. See Henry's Law. -
Rb Sumps- Custom, Off Shelf, Back Yard Jobs
Kevin Johnson replied to humz's topic in Forced Induction Performance
I remember reading this thread last year. I finally had time to complete working on an RB26DETT that had been sent to me last Summer. This info has been posted in another thread but this one is most appropriate. With respect to the RB26DETT sump with the differential attached, I would suggest first, make sure the engine is sitting level in the bay with respect to the pavement. The rear of the pan that I examined had witness marks that indicated it was tilted rearward and oil was pooling there. This situation will encourage oil to be churned by the rotating assembly. Once the percentage air passes 30% cummulative rod bearing damage will result. This engine was one of the JDM exports in still excellent running condition so I do not think the situation was an aberration. The other thing that I suggest doing would be to remove the "corporate" hump in the rear of the pan that gives access to remove torque converter bolts. Obviously this mod is for people using manuals. Oil witness marks in the pan indicate a serious pressure and windage disturbance from this protrusion that extends the length of the engine. This compromise was forced onto the engine designers. Get rid of it. The KA24 truck engine did not have this but the KA24E and later engines, including the SR20, QR25DE, etc. did. If you closely examine the windage/pumping engineering cues on the SR20 you can see what a nightmare this presented. It is plain that Nissan went way beyond the norm with this design. It has three levels of windage trays. I should point out, though, that the hump makes sections of them inoperative. How many stock engines can you name that have a kick-out with three separate parallel chambers. Before you answer that, reflect carefully on why they did this. There was a reason. If you plan on lopping off the tranny then I suggest making a dummy axle tube and welding it in place of the original. -
Kevin Johnson started following Rb20det/rb25det/vg30det Turbos and Rb Sumps- Custom, Off Shelf, Back Yard Jobs
-
Oil Control In Rb's For Circuit Drag Or Drift
Kevin Johnson replied to Sydneykid's topic in Forced Induction Performance
I should mention that if you examine the head drain passages in an old Honda D15/16 head you will see that some have no lip while others do. This biases their function to oil drainage versus blowby passage. It is best to draw blowby away from the crankcase proper in any event. Look how Ford did that with the Zetec E. There are many compromises in engine design and you can see that at least some of them are packaging restraints. -
Oil Control In Rb's For Circuit Drag Or Drift
Kevin Johnson replied to Sydneykid's topic in Forced Induction Performance
I think people miss a lot of information by cleaning parts before examining them. The RB26DETT clearly suffers from the same issue that affects the SR20 -- the projection of the torque converter access hump into the girdle. I don't pull this stuff out of thin air. Toyota faced the same engineering issue with the 1ZZ and converted the 3-4 bay axial windage rotation into a horizontal rotation parallel to the pavement. The engine that I examined also showed evidence of pooling oil in this area for an extended period of time -- that means the attitude of the engine was tilted rearward beyond the angle of the floor in the sump -- however slightly, it doesn't matter. It is very plain that Nismo went to a great deal of trouble to design the wetsump. I am very sure that they would not introduce an angle of repose in the rear of the sump that would actively collect and subject pooled oil to the churning of the rotating assembly. After all, this is the exact failure mode of the Toyota ZZ engines when the 1G wetsump rating is exceeded. Talk to some windage engineers at the OEMs -- they examine oneanother's designs. I think the root cause is old engine and tranny mounts. -
Oil Control In Rb's For Circuit Drag Or Drift
Kevin Johnson replied to Sydneykid's topic in Forced Induction Performance
Set the pressure relief valve to 12 inches Hg as a good compromise. -
Rb20det/rb25det/vg30det Turbos
Kevin Johnson replied to clip14's topic in Forced Induction Performance
You might want to ask over on Turbo Dodge. If I recall correctly, Chrysler/Dodge produced more turbocharged engines than anyone and those turbos were meant to last for the duration of a drivetrain warranty. That's a huge database of empirical info even though it is dated. I think the water protects the bearings on shutdown by boiling/cavitating instead of allowing temps to reach oil coking levels. I am not an expert in this, just saying it doesn't hurt to ask. -
Oil Control In Rb's For Circuit Drag Or Drift
Kevin Johnson replied to Sydneykid's topic in Forced Induction Performance
Hi Duncan, I apologize for the big delay but I have been super busy. If you look at the oil witness marks carefully you can see a huge triangular shaped effect that extends from the rear to the front of the engine. Get rid of the hump. It is very obvious that an incredible amount of thought/serious-engineering went into the RB26DETT wet sump. What would I suggest? Get rid of the hump -- that was imposed on the designers. Make sure the engine sits level or very slightly tilted forward with respect to the pavement. The pan clearly indicates that oil pools in the back of the pan otherwise. This will destroy your engine in short order. I suspect this is also the genesis of the need for head drains. Old engine and/or tranny mounts might be to blame here. I designed a scraper for the engine that removes oil on the downstroke prior to entering the complex triple layer windage tray setup. If you modify the sump by removing the trans, I would go so far as to make a dummy axle-section and weld it in there. Some pics of the scraper in situ; OEM components removed for clarity only, RB25 design is similar but covers more of the rotating assembly because the block casting is different: -
Oil Control In Rb's For Circuit Drag Or Drift
Kevin Johnson replied to Sydneykid's topic in Forced Induction Performance
One of the restrictions on the efforts of the Nissan engineers was/is the "corporate" hump in the rear of the oil pan. This hump is present to allow easier access to torque converter bolts (I was told this and assume it is correct). The hump creates a large problem because under high G conditions the oil naturally migrates to the rear of the pan. The volume that the hump displaces and its ramping effect create a churning zone for oil where the oil becomes highly aerated -- this is also the principal drain zone for the heads. Get rid of the hump. If you carefully examine the engineering on the SR20 you can see the problems the designers had with the local high pressure zone created in the 4th bay by the hump. Increasing the amount of oil in the pan is problematic because at the G-limit of the design the excess oil naturally migrates to this same zone. This situation parallels the failure mode for the Toyota 2ZZ engine in the Spyder and Elise, both of which can exceed the 1G design limit of the stock pan. The high aeration of the oil causes the failure of the Geroter pump. If the pump can withstand the aeration then the problem would shift to the first rods to receive the mixture. In the Porsche 928 and 944 engines this lead to the classic 2/6 rod failures. Looking at the Tomei drawing of the oil circuit it looks like rods three and four would be hit. Failures of the number 6 cylinder would likely be due to localized overloading of the ring pack and detonation or incipient detonation. Because of the hump there is no windage control in the last bay. A good solution to this would be a dual pump as in the BMW M3 (S50 engine) where the secondary pump could scavange from this zone and transport the oil back to the sump well. This is passing into the transition from wetsumps to drysumps. The Porsche integrated drysump takes this a step further (a type of active wetsump). I only have an RB26DETT pan (with AWD) to look at. In this pan, the witness marks from the oil indicate that it normally operates with 2 quarts or liters resident in the sump proper, the balance being in circulation. This is a fairly typical amount. -
Oil Control In Rb's For Circuit Drag Or Drift
Kevin Johnson replied to Sydneykid's topic in Forced Induction Performance
The restrictor gives lower oil pressure in the galleys for the lifters. This lower pressure allows entrained air in the oil supply to coalesce and interfere with lifter operations. Under higher pressure in the circuit prior to the restrictor the bubbles are smaller. This decrease in size is one of the reasons high pressure is used in oil circuits. If you are running mechanical versus hydraulic lifters restricting the oil supply to the head is less problematic with respect to entrained air. -
Oil Control In Rb's For Circuit Drag Or Drift
Kevin Johnson replied to Sydneykid's topic in Forced Induction Performance
A restrictor valve to the head can lower the pressure in that portion of the circuit.