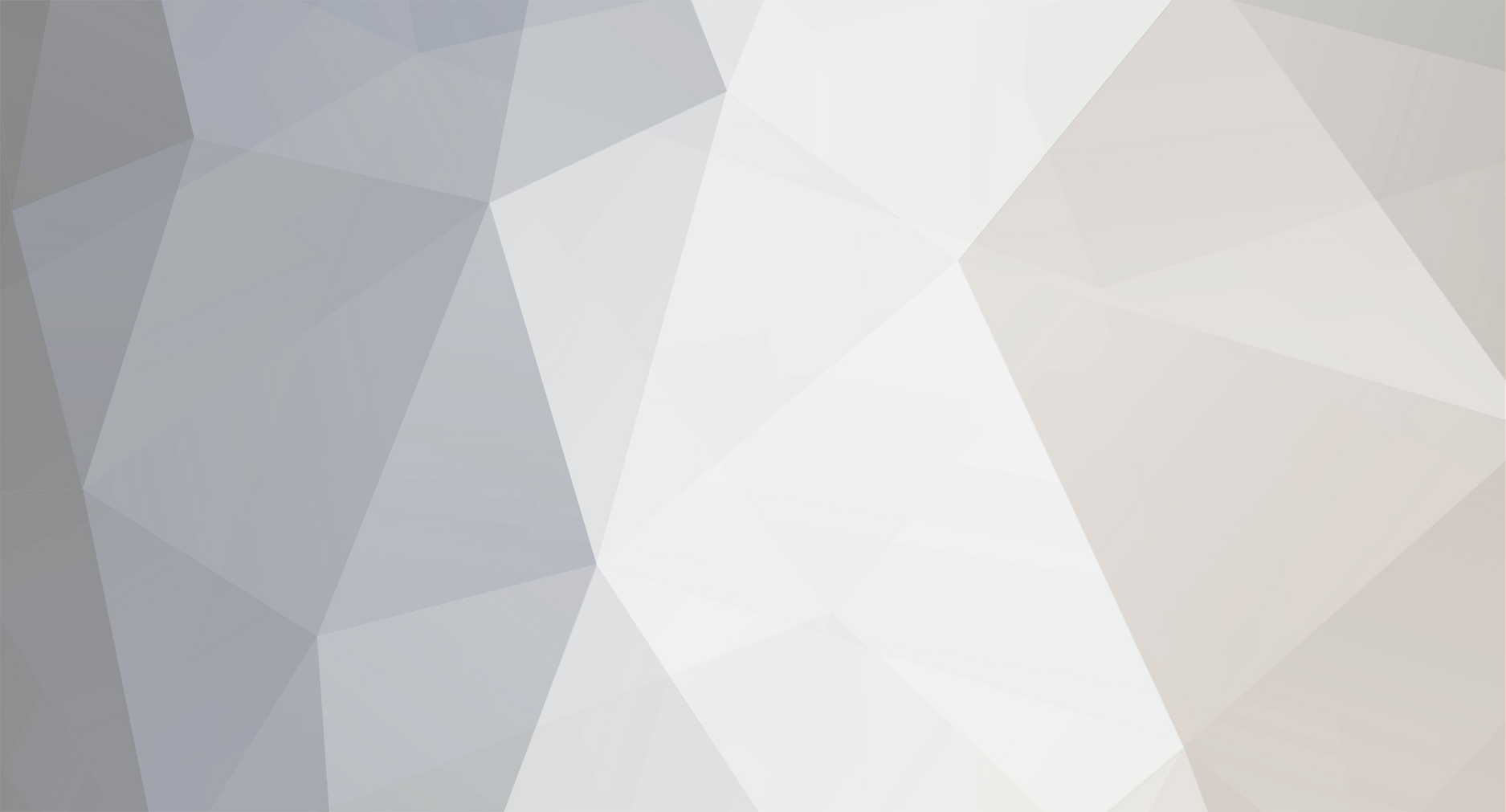
ZimNismoBoy
Members-
Posts
103 -
Joined
-
Last visited
-
Feedback
0%
About ZimNismoBoy
- Birthday 08/09/1982
Profile Information
-
Gender
Male
-
Location
zimbabwe, Africa
Profile Fields
-
Car(s)
R34 Gtr Vpsec II Nur
-
Real Name
Adam Saiyad
ZimNismoBoy's Achievements
-
Diy R34 Manual Conversion Using R33 Parts
ZimNismoBoy replied to E_Lu-SHuN's topic in Tutorials / DIY / FAQ
no no you have some of your info incorrect, the Coupe and Sedan use the same propeller shafts, the only difference comes in the length of the front half of the shaft and the number of splines on the inside of the prop shaft or tail shaft section as its called ( the front half ) so essentially I want to know what have I got to do to make the front half of the tail shaft work with these in hand . The Yoke and Flex joint section of the front half ( been cut by the breakers in japan using a blow torch ) And the front half of the auto box prop shaft with the smaller Yoke attached ? Cheers thanks again -
Diy R34 Manual Conversion Using R33 Parts
ZimNismoBoy replied to E_Lu-SHuN's topic in Tutorials / DIY / FAQ
been reading and have found that the auto drive shaft is longer then the manual drive shaft ? Please advise which is longer and which is shorter ? Would like to know . if the auto is longer then its easier to weld the Yoke section and UJ on to the shaft . -
Diy R34 Manual Conversion Using R33 Parts
ZimNismoBoy replied to E_Lu-SHuN's topic in Tutorials / DIY / FAQ
I have some technical questions . When you say auto rear to manual front prop are you talking about the two halfs meaning a complete front half from a manual onto a complete rear half of auto? Or are you speaking about joining the Universal joint of the manual prop onto the auto prop section .... meaning the yoke off the manual onto the auto prop joining the two UJs together ? Did the shop that did your conversion use all four bolt holes of the body section or only two ? I need to know for sure before I go ahead would like to drive it out the garage the same day I do the conversion and not be stuck ..... Im miles away from any breakers we don't have many of those cars here . And ordering would take ages online ? Thanks in advance Adam -
Diy R34 Manual Conversion Using R33 Parts
ZimNismoBoy replied to E_Lu-SHuN's topic in Tutorials / DIY / FAQ
Hello Gents, I have my box and about to commence on the conversion . A question I need to ask on the ER34 GTT auto to manual . I have the gearbox but no cross member . Do I just need to change the cross member gearbox transmission rubber mount to the manual one to get it to mount on the bolt holes correctly? don't want to use the two bolt mounting method would like to mount it with 4 bolts as originally intended . If I change the rubber mount will it line up correctly or is the auto chassis adapted only to the auto cross member ? Secondly I have the yoke section of the front half of the tail shaft its been cut but we can weld the yoke if need be . Confirm what is the length of the front half prop shaft on the auto ? Confirm what is the length of the front half prope shaft on the manual R33 ? Please help so I know if can cut weld and balance the front half prop shaft to install in my conversion? thanks in advance . -
ZimNismoBoy started following Diy R34 Manual Conversion Using R33 Parts
-
Any One Fitted A Walbro F9000267 E85 Fuel Pump
ZimNismoBoy replied to ZimNismoBoy's topic in General Maintenance
why did Nissan have to go and make the gtr tank so different, I don't have a cradle for a GT-t and no access to one but let me know if this works and I will have to make a plan to get one .... tut tut any one else fitted one and managed to get a away with a install in the stock location with a long hose going into the tank with remote sock ? I presume the pin holes are there for lubrication etc ? and it being a intank pump will need to be submerged to work properly ..... what a pain -
Any One Fitted A Walbro F9000267 E85 Fuel Pump
ZimNismoBoy replied to ZimNismoBoy's topic in General Maintenance
a bit concerned any one else done the conversion ? at this stage id be more inclined to go with a uprated nismo or tomei pump to feed the need for the e85 fuel as it seems more a likely replacement for the stock location and plugs but also because of the fuss of the bottom hose to sock connector ? -
Any One Fitted A Walbro F9000267 E85 Fuel Pump
ZimNismoBoy replied to ZimNismoBoy's topic in General Maintenance
Many thanks for that, So it fits ok no worries no problems, just need to find a way of not cutting the original Nissan fuel pump connector off, don't really want to as I might one day want to put the original back inside, so need some backward compatibility . And under normal conditions the pump has the male end of the connector built into it ....... Any ideas on that part ? From what I can tell the bottom of the pump from walbro has a foot sock attachement with a normal circlip crimp that pushes over the exposed stud, does this mean that the pipe comes with this sock/foot type attachment with a crimp style connector ? -
Hello all just wanted to check i wanted to purchase a Walbro e85 fuel pump part no F9000267 and also get a fitting kit 400-0085 as well to install into my Nissan skyline gtr 34. Can any one confirm that it can be done what about piping and remote pick up with the sock as i know the gtr 34 has a fuel pump that sits high and has a remote hose that has a sock for intank fuel pick up from the base of the tank . Will await to hear your answers. thanks in advance
-
Hks Evc Diy Repair If You Dare :)
ZimNismoBoy replied to ZimNismoBoy's topic in Forced Induction Performance
Hi all will post some pics, but i must confirm this and make sure you have all heard it loud and clear the motor inside will never ever fail because it has very little moving parts no brushes that can fail and no moving parts bar the corkscrew type pin in the center. Now to confirm with the one comment i will say this, the stepper motor doesnt compress air it controlls the air from the intake manifold and the pressure developed by the tubbies is then redirected into the boost contoller and the corkscrew thingy has a needle and seat that allow a certain amount of air to by pass but also allows a cetain amount controller amount to the waste gate actuators opening and closing them to give a precise boost . These boost controllers are like no other they are the only boost controller to use a stepper motor and they are very very precise and very stable too thats why the stepper motor that controls the needle agaisnt the bleed seat is better then a solenoid valve. Imagine this the first carbs didnt have a solenoid to control the fuel flow, they had a needle and seat on a float so imagine this being the same principle for the HKS evc boost contollers that use the special stepper motor . To give an example of precision they use stepper motors in CNC small scale machines and they are really accurate . I will try and make a how to ? Dont know how good i will be as i have done most of the work already and will need to disassemble my evc 4 but its ok its all in good faith . So keep the filters clean keep them in place and your controler will last a life time, get dirt in the stepper motor and you will kill the motor quickly . I sure hope we can find a good source for the motors then we can get fixing . Any one have any evcs they want to donate that are faulty so i can prove the theory!!!! But wait i still need to post a pic of the stepper motor so that we can start searching for a suitable replacement ,. -
Hks Evc Diy Repair If You Dare :)
ZimNismoBoy replied to ZimNismoBoy's topic in Forced Induction Performance
lol you know i really didnt think i was a nerd but i am prepared to do a full how to guide just to help everyone else out . I am currently looking into motors and i need the aid of the electronic gurus on here . From what i can tell the motor is a 2 phase 6 wire or 5 wire motor . Dimensions are 25x15 width is 250 mm x 150 mm im looking for a suitable replacement on alibaba and if i can find one then we all will have a field day knowing that the only part that can become faulty because of dust can be repaired . Im struggling to find a stepper motor with the internal diameter that will allow the spindle to be pressed in . -
Hello fellow enthusiasts. So after 3 years of the car being a rebuild i have it running and rebuilt and finished the run in process. So was tempted to switch on the boost controller 1900 kms down the road. So flipped the switch and monitored boost pressures with a keen eye and eerrrm no change boost was same as factory stock 0.65Kpa blaah so tried readjusting boost settings A and B and tried resetting all settings and no change so a boost controller departed the technological living . So opened it up and gave it a good looking over found the magic STEPPING motor and inspected for free movement and all seemed fine so oiled it assembled and tried again with a test drive and still no boost .. So came back and decided to open it and feed some air into the Map sensor for boost that comes from the intake manifold it connects to the B line on the three pipe outlet/inlet and tested with a small syringe connected to a pipe directly feeding compressed air into the port and check the stepper motor for movement and nothing ..... so its dead . So went hunting for a motor nothing available. Now dont get me wrong this isnt a bad controller its a 2001 hks evc 4 and it works like a dream up until the time it might have gotten dirt inside and stuffed the motor . So i found a old hks EVC III stepping motor unit and opened it and low and behold the magical stepping motor was inside . so i cut it as far away from the wires of the stepping motor as i could and there was 6 wires in total . black and Red x2 and Brown and yellow and orange i think. So i cut the stuffed motor out of my nice evc 4 control motor box and got some heat shrink tubing. 1mm . Soldered in the new motor making sure i had heat shrink on all the wires before i soldered them in place. And carefully and i mean CAREFULLY inserted the motor making sure the pin was located in the slot inside the casing as this alows the bleed pin to float upward and downward inside the motor housing and essentially bleeds off air. Now inside the unit it looks very and i mean very similar to the hks EVC III unit and has two MAP sensors that measure actual manifold boost and actually waste gate boost its a really good system. So now i have soldered in the motor and heatshrinked all the wires and installed it with the pin in place and connected it up to my boost control unit as before and low and behold we now have a working boost controller. i tested by setting a low boost pressure and closed the unit up. I then fed again into the B pipe some pressure using the syringe. I think blew using my small lungs lol into the I port and checked for a bleed off point and listened for the stepping motor to purr away as it moved the pin upward and down into the top seat and bottom seat. I then checked high boost by setting a high setting close to 80% that of stock boost. I then pressurised the B port again . And blew into the I port and waited for a bleed off and only at a really high pressure was i able to pass air through the I port, it will be closed at idle or minus boost and will not allow air through until the desired boost is reached. If we can find a good source for the stepping motors we can definitely repair them and save an easy few penny 700 USd for a new one EVC 6. However i dont see any harm in using a older unused version of the Hks Evc series to repair a newer version . Dirt kills these motors always always use FILTERS on the I and B ports as they are fed ports meaning air passes into them . And this contaminated air could be carrying fine dust that can lock and seize the stepping motor inside . Just to give some insight the motor has some bearings These ball bearings give the motor its long lasting life span . Infact from research the motor was never designed to ever fail based on how the cork screw mechanism is designed inside the stepper motor . If necessary i can post pics as well. Im still yet to go on a test run and confirm that it is repaired. but im certain from my testing that the motor is ok and that it will control boost the way its supposed to. For the last warning i give please make sure you dont tug on the stepping motor wires they are soldered internally and are very very weak and can snap off in a flash . Dont remove any Gum or glue around the motor area or on the outside the gum is there to protect the circuit board from moisture. And the Glue behind holds the sensors flush so that they dont leak boost pressure . Remember this boost controller has a before and after MAP sensor . So these boost controllers are so accurate and potentially failsafe. If any one needs pics please let me know i tried to take as many as i could . and i can post them just really tired after soldering and heatshrinking the wires. The heat shrink is to ensure that we dont use insulation tape and also ensures that each soldered connection doesnt come out . On the Evc board close to the red LED there is a resistor that has a split wire with each half neatly placed next to the LED on either side . Leave it disconnected it was done at the factory heavens knows why . If any one else has had any experiences with the Evc stepping motor please do share this will be great to get out there and help others who may have resorted to using a manual bleed valve or Dawes device lol.
-
Looking For A Rb26 N1 24U Block New Or Slightly Used
ZimNismoBoy replied to ZimNismoBoy's topic in Wanted to Buy
if any one else needs a new block give me a shout have the contact details and am willing to share ... -
ok as of yesterday i have confirmed weird results but this is how it goes. Across the board all 6 cylinders are 0.45mm on the top ring <======= TOP RING Across all 6 second ring is 0.45mm <===== SECOND RING And these are new rings going into a new block ??? i dont understand how come they are so big ? has nissan decided to make the gaps bigger ? So that you dont run the small gaps on a small bore ? I dont get it ?
-
sorry this post above is going off memory for the clearances i need to check with the paper i wrote on and make sure i have the right readings please hold fire on ring gaps let me get the actual readings and will post them up as far as i know the second ring gap falls in the tolerances but the top one is too wide and doesnt even meet the max ring gap ....listed in the manual .
-
inherently thats what i have 0.0024" or 0.063 mm across all the mains and i would expect it is a loose fit but having a tomei oil pump will help as the stock rev limit is 8400rpm. On a second note the ring gaps .... Top ring Chrome ring has a clearance of 0.50mm Second ring has a clearance of 0.45mm measured again . 8 sorry im new to the terms and measurements please forgive any errors as measuring and using .00's is never been what im used as i dont work with engine everyday or measuring tools lol. thanks for the input