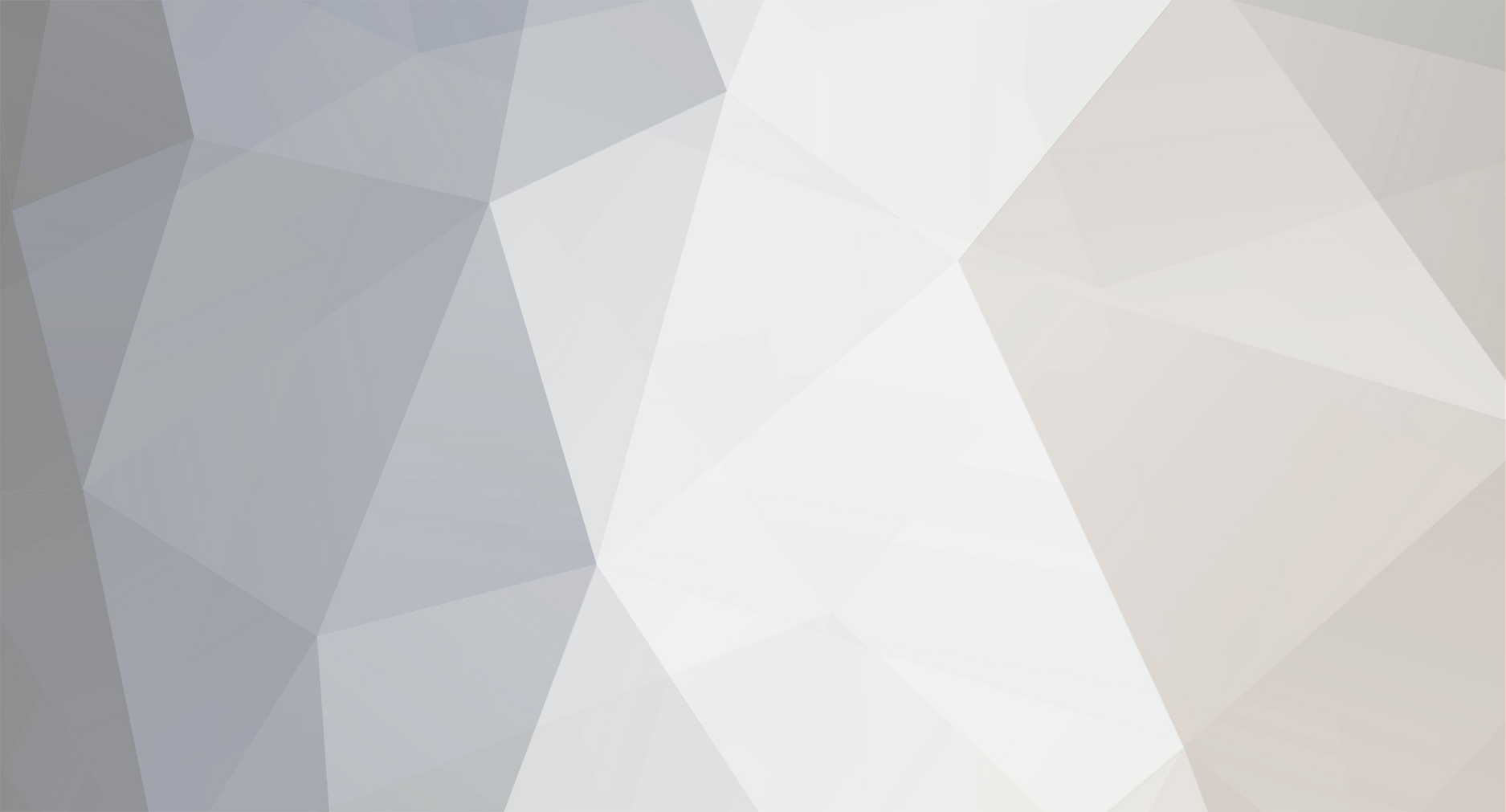
dorifticon
Members-
Posts
266 -
Joined
-
Last visited
-
Feedback
0%
Content Type
Profiles
Forums
Events
Gallery
Media Demo
Store
Everything posted by dorifticon
-
Andrew's R32 Gtr With Forged Rb30Dett Build
dorifticon replied to dorifticon's topic in Projects, Overhauls and Build-ups
Even with the engine dummy installed in the car (ie the long motor) and ensuring the timing belt cover doesn't foul on the bonnet, that's not the end of the problems. The twin-turbo pipe also fouls. This may be why many of the GTR rb30 conversions seem to also have a single turbo conversion, with custom pipework. The solution was to grind off the boss for the "twin turbo" sticker and then took up the rest with washers in the rear bonnet hinges. It aint pretty but it works. Kinda. -
Andrew's R32 Gtr With Forged Rb30Dett Build
dorifticon replied to dorifticon's topic in Projects, Overhauls and Build-ups
So there were some more screw-ups along the way. This picture illustrates the problem getting the intercooler plumbing to line up, and then the solution - just inserted a section of 3" pipe with a bead welded on and some hose clamps. Same solution for both sides of the engine bay. There's also a long piece of rubber or silicone pipe required for the bov connections. -
Andrew's R32 Gtr With Forged Rb30Dett Build
dorifticon replied to dorifticon's topic in Projects, Overhauls and Build-ups
Even after the major issues have been tackled, there are still a multitude of annoying little things that need to be sorted. Here is a list of them: -Timing belt cover - even using the rb30 lower timing belt cover leaves a 38mm gap. I will probably tack weld on a bit of sheet to bridge the gap. -twin turbo support brackets - there is no provision for the alloy braces that sit below the turbos (mounted off the dumps). Haven't figured out how I will address this yet. -new oil drains required off turbos - for the additional block height and also because a t-piece is needed to run 2 oil drains into one block mounting boss. Also if you are running an oil drain from the back of the cylinder head (not an issue unique to rb30's but anyway) a further t-peice is required. -New oil and water feeds for the turbos are required as the stock ones won't bend far enough. I got braided lines from ebay (big props to eiji takada!) -knock sensor mounts - there is provision for 2 knock sensors but the mounts are different thread diametre and pitch to the ones on the rb26. An adapter is required. -the rear oil drain needs to clear the hard vaccuum and water lines at the back of the head. I "modified" (hacksawed) the bracket on the driver's side. -the rb26 power steering bracket needs to be modified. You CANNOT use the rb30 one, it is different (I tried). -the rb26 cast iron exhaust flanges need to be ground back to clear the rb30 block (assuming you didn't mod the block) -there are a couple of heater hoses and the diff brether hose that needs to be replaced on the driver's side due to the extra distance between the plenum and the bottom of the motor -the crank bolt and washer from the rb26 doesn't fit the 30 - an rb30 one is required. All in all it's a lot more screwing around than I realised. The problem is you don't really know there's a problem until you attempt to install x to y and realise you need z. Then there's delay getting the part, which all kills the motivation really, especially when you're working after hours and weekends on the thing. Had I known at the outset, I really would have built a 2.8 stroker with the 2.6 block. Oh well, live and learn. -
Andrew's R32 Gtr With Forged Rb30Dett Build
dorifticon replied to dorifticon's topic in Projects, Overhauls and Build-ups
Well, it's been slow going, mainly due to delays getting the balancer and timing belt, but the work has been progressing. One of the tricky issues was spacing the engine down to get sufficient bonnet clearance for the taller motor. Here is a pic of the steel spacer plates I and a mate made up to sit between the rail and the k-frame. I may do a more detailed write-up with the dimensions etc once the install is finished. Also I ended up going with a (good condition) second hand HKS triple plate clutch - should hold the extra power better than the OEM one that was in there. -
Hey all Just in the last stages of finishing an RB30/26 engine build, and as many of you would know the RB26 power steering bracket top bolt goes to the head, whereas the rb30 one bolts to the block. Rather than grinding off the boss on the rb26 bracket, I was hoping to be lazy and just put on a rb30 one. So let me know if you have one laying around that you'd like to sell cheap - best way is to shoot me a txt on 0415 838 790 because I'm not on here much. I'm in canberra so if you're interstate I'd need postage as well. Cheers Andrew
-
Hey Just wondering if anyone manufacturers subframe spacer kits to drop the subframe on the R32 down to accomodate the extra deck height; and to space the mounts up to accomodate the sump adapter? Have done a fair bit of searching and can't find any retail options. If anyone has any pics of their adapters that would also help. Cheers Andrew
-
Thanks for all the replies. Just to be clear, it's a fully balanced and blueprinted, forged rb30 build - the workshop says it is fine up to 8,500 rpm, so it will be revving a bit higher than your standard VL commodore, for example. Valve train and turbos definitely won't be holding back the revs. I am currently tossing up ideas to mount something into the sump itself with a bracket of some kind but am concerned it may not be secure enough to handle vibrations etc.
-
Andrew's R32 Gtr With Forged Rb30Dett Build
dorifticon replied to dorifticon's topic in Projects, Overhauls and Build-ups
Thanks mate, I hope so. It's had budget blowouts that would make SOCOG proud, but as we all know that first time you drive it, when it's all run in, and just floor it and hit boost... makes you forget about the gaping hole in the wallet. -
Andrew's R32 Gtr With Forged Rb30Dett Build
dorifticon replied to dorifticon's topic in Projects, Overhauls and Build-ups
Getting the damn engine out was a mission and a half. We reviewed all the hints and tips on the net, but really accessing those two top bolts for the motor seemed impossible without moving the engine/motor assembly forward. We ended up taking off the front turbo (was a lot easier since it had been off not long ago, and we retapped/antisiezed the studs and nuts) as well as the power steering, A/c, and alternator. Then we ripped the engine mounts out of the car completely (secured the motor with a crane). We also undid the gearbox mounts and both prop shafts, and let it rock down slightly. We slid the motor forward to undo the top 2 bolts, then secured the gearbox in place with a trolley jack (we were still able to angle the front upwards). Once the starter motor was out, we undid the rest of the bolts and slid the motor forward and out. It was a time-consuming task and I broke one engine mount in the process, but she came out in the end. If I could have done anything differently, though, I would have removed the engine pulley, just to get a bit more clearance between the radiator support/Aircon condenser - once the prop shaft was out we couldn't stop the motor from turning over. So now the r32 sits, waiting for a new heart... -
Andrew's R32 Gtr With Forged Rb30Dett Build
dorifticon replied to dorifticon's topic in Projects, Overhauls and Build-ups
The obligatory forged slugs - these will maintain the standardish (for the rb26 twin cam head) static compression ration around 8.5:1. Also the machined crank. It's been balanced, as well as the galleries sized and micropolished. Being an RB30 crank, I of course had the wider oil pump drive collar pressed on. Hopefully, in combination with the nitto pump, I will be able to maintain strong oil pressure. The clearances are slightly higher to run a heavier oil. -
Andrew's R32 Gtr With Forged Rb30Dett Build
dorifticon replied to dorifticon's topic in Projects, Overhauls and Build-ups
I am running a nitto high-flow oil pump, as well as forged nitto rods. I was particularly keen to run forgies given the extra side loads created by the increased rod length and angles, and since the motor is going to be seeing fairly serious boost. These particular rods have a special provision in the side to spray oil onto the thrust side of the bores. Hopefully this will offset any effects of not running piston oil squirters. -
Andrew's R32 Gtr With Forged Rb30Dett Build
dorifticon replied to dorifticon's topic in Projects, Overhauls and Build-ups
The RB30 blocked back from machining - cleaned, crack tested, decked, bored/honed and tunnel bored. It has also been drilled and tapped to run 12mm studs, and the timing belt tensioner has been relocated. -
I see someone has already asked this but I couldn't find a response. Basically, I have my RB30 bottom end back from the workshop, and it's running the RB30 girdle which has no provision for a windage tray. It seems like it would be *possible* to drill and tap the girdle to fit the windage tray but I just wanted to know whether people are bothering to do this or whether people are running their RB30 setups without the trays (is it even possible? Does it foul on the crank?) All things being equal I'd probably like to run them but this would entail dissassembling the entire bottom end in order to drill and tap the girdle (otherwise I would be risking swarf going into my bottom end). Any advice (particularly on the risks of NOT running the windage tray) greatly appreciated. Andrew
-
Andrew's R32 Gtr With Forged Rb30Dett Build
dorifticon replied to dorifticon's topic in Projects, Overhauls and Build-ups
Here is a shot of the drillings opened up. Obviously stuff rags into to the driveshaft openings, don't want swarft going all through the bearings and diff. And then give it a real good hosing to get rid of any swarf. Here's the baffles installed - I put a dab of high-temp loctite on all the bolts, don't want anything working it's way loose down there! -
Andrew's R32 Gtr With Forged Rb30Dett Build
dorifticon replied to dorifticon's topic in Projects, Overhauls and Build-ups
So, I have acquired a separate sump and transfer case for building the rb30 long-motor. I decided to run with the tomei gated sump baffle. As the name suggests, it has a series of gates surrounding the oil pickup to keep it immersed in the oil and prevent oil starvation under high cornering loads/launches/braking. The instructions specify that the existing drillings in the sump (which are basically pinholes) need to be drilled out to 5mm. This requires some dissassembly of the sump assy to get the drill in there, in particular removing the passenger-side driveshaft oil seal and removing the driveshaft and pipe. -
Hey all Just wondering if anyone has any cheap cam covers and/or upper and lower timing belt covers from an RB26. The condition doesn't really matter, just want to bolt them on temporarily to transport a motor. Dunno if the RB25 cam covers work as well, if so those are fine, BUT ONLY IF YOU KNOW FOR A FACT THEY BOLT ON. So if you have a set of rough/dented/scratched cam/timing covers sitting around that you wouldn't put on an engine, let me know. Located in ACT, if posting just chuck 'em in a box and send. Best to give me a call on 0415 838 790 cause I don't always get onto the forums. Cheers Andrew
-
Hi all Am in the process of building my RB30dett, and am assembling full long motor separately and then going to do changeover. I am currently working on the sump. After a bit of searching on this site, I settled on the tomei gated sump baffle, which I purchased. Unfortunately the instructions are in japanese. Most of it I worked out, including opening up the oil drain holes in the sump to 5mm diametre by re-drilling (after removing diff oil seal and dismantling the driveshaft pipe etc) There are basically two peices in the kit, there is the "box" section with the gates that goes at the bottom, and the flat bit that sits on top. Now, the box section has notches cut into it where the bottom of the box sits against the floor of the sump (there are gussets or ridges in the floor of the alloy sump and the notches accomodate these). But there is still at least 2-3 mm clearance in many sections between the bottom of the box and the sump floor. Am I supposed to use some kind of sealant between the box section and the floor of the sump to ensure no oil can get through? There is some diagram in the pic which *could* indicate sealant but it's not hugely helpful. It seems like the type of thing that would heat up and you'd have strands of sealant floating around in the bottom of the sump, but if the instructions say to do it then I'll do it. Or do you just bolt it in?
-
Hi everyone My r32 GTR has been featured in Autospeed. It represents a lot of work over the past year or so, and there will be more mods (and hopefully articles) to come. But it is also my journalistic debut! Please show your support by rating the article (via the rating key below) and tell your mates. The more hits the article gets, the better the chance of future articles! Also please let me know what you think by posting below. My r32 GTR featured in Autospeed Cheers! Andrew
-
Andrew's R32 Gtr With Forged Rb30Dett Build
dorifticon replied to dorifticon's topic in Projects, Overhauls and Build-ups
My car has now been featured in Autospeed! Autospeed article - Andrew's r32 GTR It's also my first byline! Please support by rating the article and passing on to anyone you know who may be interested. Cheers Andrew -
Andrew's R32 Gtr With Forged Rb30Dett Build
dorifticon replied to dorifticon's topic in Projects, Overhauls and Build-ups
So $120 in total - that's a pretty serious hourly rate given I reckon the full job could be knocked over in 30 mins. To put that cost in perspective, a very nice air die grinder and tungsten carbide bit (which flies through cast iron) cost me a total of $200, and I get to keep those tools which have come in useful a number of times since... In terms of the skills, I hadn't ported anything before I did my manfolds and I reckon i did an ok job. In fact it is a great opportunity to get some practice and build confidence using an air grinder. My tip would be to work in the opposite direction of the way that the bit is rotating, and don't use too much pressure, just be gradual about it. And cover up/move anything in your garage/shed that you don't want covered in a fine spray of cast iron filings! -
Andrew's R32 Gtr With Forged Rb30Dett Build
dorifticon replied to dorifticon's topic in Projects, Overhauls and Build-ups
So just out of curiosity, what are you getting charged for them to remove and replace a set of turbos? The labour cost must be significant - it took me and a mate a full weekend of working together to do the full job, and we're no slouches when it comes to that kind of thing. Also, what killed your HKS turbo? I thought they were pretty robust? Oil flow problem? -
Andrew's R32 Gtr With Forged Rb30Dett Build
dorifticon replied to dorifticon's topic in Projects, Overhauls and Build-ups
I didn't really port them as such - I really just matched the turbo flange to the turbo's (ie removed the lip on the manifold). All up maybe 15 minutes per manifold? When I bolt them up to my new cylinder head, I will have to match up the actual runners to the exhaust ports, which will take much longer, but will post up details when done. -
Andrew's R32 Gtr With Forged Rb30Dett Build
dorifticon replied to dorifticon's topic in Projects, Overhauls and Build-ups
In terms of the block, after much soul-searching, I decided against a 2.6 build, and against a 2.8 stroker kit (although the billet cranks that come with those kits are sooooo tempting... and retaining the OEM block!!!). I have decided to go the rb26/30 route. Also, rather than actually build the bottom end myself, I am going to get the bottom-end rotating assembly put together by a workshop, then bolt head, sump and ancillaries on and do the install myself. This is more for pragmatism than anything else - I would like the build done some time this century! As with the previous round of modifications, the build will be overkill for the power I achieve in the short term, but the plan is to build the bottom end once and build it right. I have been in contact with heaps of builders, and they all have different ideas about various aspects of the build. There are heaps of variables with the RB30 block - which studs/bolts to use, to o-ring or not, to grout or not, what girdle to use, oil squirters or not... There are also heaps of additional costs that just don't happen when sticking with the OEM block. Sump adapters, oil drains, machining, etc etc. Will post up final details of the build specification when complete, and hopefully some quick explanations of why I have gone the way I have. But regardless, with a bit of extra displacement, a fresh motor and head, some lumpy cams and porting, hopefully it will achieve a decent power increase while still retaining *some* semblance of driveability. And if not... oh well, the datsun is a good daily. -
Andrew's R32 Gtr With Forged Rb30Dett Build
dorifticon replied to dorifticon's topic in Projects, Overhauls and Build-ups
Well, with Phase I of the build now complete, it is time to move on to Phase II - the motor itself. I have made a good start with assembling parts. I purchased a complete cylinder head from a forum member, including cams (JUN 272 deg, 10.5mm lift) and springs, as well as porting. I have taken a pic comparing the stock cam profile to the lumpy ones - quite noticeable! Also here is a pic of the porting.