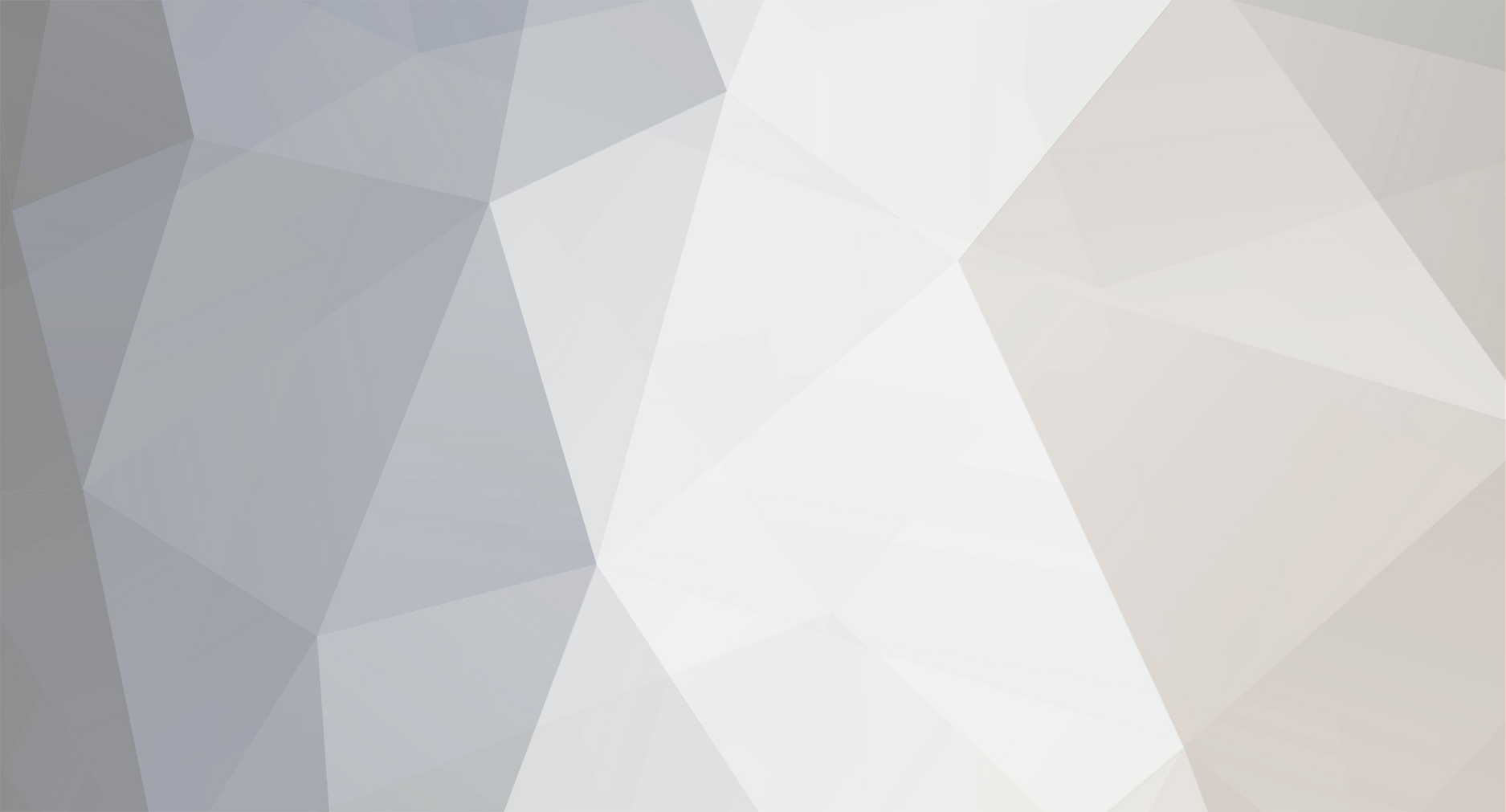
TTOBES
Members-
Posts
19 -
Joined
-
Last visited
-
Feedback
0%
Content Type
Profiles
Forums
Events
Gallery
Media Demo
Store
Everything posted by TTOBES
-
Time to cut down the tree... Bloody roadside obstacles!!
-
You can get quite high peak cylinder pressures if your motor is idling too slow. At higher revs, in the time taken for the mixture to burn, the piston moves down the bore increasing the chamber volume for the expanding gasses to fill. This lowers the peak pressure. At idle the piston does not move significantly in the time taken for the mixture to burn so, even though there is not a huge air/fuel charge in the cylinder, it has a much smaller volume to burn in and the peak pressure can be significant. This may be why the knock values dropped somewhat when you increased the idle. Food for thought...
-
There is also a pdf file in each of 'Cubes' posts that summarises the whole process...
-
Try reading this thread http://www.skylinesaustralia.com/forums/t15420.html Your question is answered in the first few pages...!! Yes I know it's hundreds of pages long, but it contains all you need to know about building a RB30DET and, if you are serious about the build, its a must read...
-
I have been told that chrome parts can hold in more heat. Have been advised against using chrome sumps and trans pans for that reason. I would assume that polished parts would do the same. Most standard radiators are painted black... Don't know about powder coating, as it is a relatively thick coating. Perhaps a paint finish would be better...
-
LOL... I'm on a Skyline forum so I have got into the habit of not mentioning that I have a.... VL Wagon (said very quietly out of the corner of his mouth while looking furtively over his left shoulder!!!!) And Ari Vartanen has nothing on me!!! One of my favorite drivers of all time, they even say that his balls are that big he has to carry them in a wheelbarrow....!! I have owened two cars in the past capable of putting 500+hp on the road. A stove hot SBC in a LX Torana that was a huge amount of fun and a HX ute with a BBC that had less traction than you can ever imagine... This time round I want to try a turbo combo with similar power in a better prepared car... I must admit, having spent the last couple of months on a bunch of Skyline forums researching this combo, that I have thought about putting a milder (read cheaper) combo into the VL and finding a GTR/GTS-4 for this sort of power. R32 GTRs can no longer be registered here so they are worth parts value only, around 10k for a nice one. My boy and I have owned two R32 GTS-Ts in the last three years and they are a superb little package... He's moving back home from Sydney at the end of the year so I'll continue with my plans till then... I still feel that this power level is ok in a capable 2wd... I think it was Peter Brock who said "Always bite off more than you can chew, and then chew like crazy..." Cheers
-
Totally agree... I had assumed we were starting with a car that had a reasonable suspension/brake package as azzr32 had described earlier. (ebach springs with bilstein shocks at the moment, r32 gtr diff with 1.5 way lsd, strut brace front and rear, full cams approved cage, sway bars, camber kit front, adj castor rods, adj control arms, bridgestone RE55S/ dunlop second hand full slick, brembo f50 calipers/ DBA 343mm rotor, etc) Using this spec as a starting point it may well be easier to ' learn to drive the car to it's potential and develope your suspension/traction as you go...' with your target hp on board. If nothing else it will show how far you need to go With my own car I have spent just over $12k on a good adjustable suspension package, a 343mm/330mm brake setup, rebuilt LSD rear end and wheels and tyres. The basics... And I'm still running around with the original 120kw... I also agree with your comments regarding getting your priorities right with the engine build. For a track car the main focus should be on building a responsive usable package, although I still believe that can be achieved around the 500hp level. Using my own plans as an example (as I think azzr32 and I are after a similar result) a forged bottom end, well preped head, the correct cams, decent manifolding and a pair of Garret HKS2530 equivalents should see the job done. I have mentioned 500rwhp only as an indication of the performance level I'm after. The priority is to build an engine with the widest, fattest torque curve possible and the best response I can achieve. azzr32 is one step ahead of me as he has the RB26 ITBs... Cheers
-
Perhaps undrivable was a bit strong... I see so many posts where someone has big plans with some fairly lofty horsepower goals and people advise them that they will never be able to put that power to the ground... To my way of thinking, unless you can fry the tyres in 5th half way down the back straight, you do not have too much power. Part of the art of racing is learning the limits of traction available in each gear in a particular situation, putting your brain rather than your ego in control of your right foot, and utilising it to the max. This is providing the motor is not a grenade and will be relaqtively reliable... How often do ypu see posts where someone has built a motor and is now looking for more power, often needing to replace expensive parts they have already bought. My advice is to set your horsepower goals where you want to end up, learn to drive the car to it's potential and develope your suspension/traction as you go...
-
So... Tell me what makes 500rwhp so undrivable on the track...??
-
The same principals still apply... The optimum amount of back pressure is none. Tube sizes are still a trade off between between maintaining gas velocity and restriction(back pressure). Turbo engines only differ in that they have a restriction in the exhaust system called a turbo. Creates significant back pressure in the exhaust manifold and chops the exhaust pulses up finely so you can't use the scavenging effect. A 3" is tried and proven. Redevil is on to it. As the man said, "a 2.25" tube will support 300hp...
-
There is a real science to exhaust tuning and the whole thing is a bunch of compromises... Here is a blurb from another forum that is interesting reading... 'Ok, this explanation may be MORE information than some want to consider but... First of all, I MUST say that backpressure is NEVER a good thing in the exhaust. By backpressure I mean resistance to flow creating more pressure for the exhaust exiting the exhaust valves to work against. Ideally you would have a vacuum at the exhaust valve and in fact that can be created with a properly tuned exhaust system. Our exhaust manifolds are NEVER going to accomplish this so my statement is for illustration only. But, consider each phase of an exhaust. If the manifold pumps into a restrictive catalytic converter (backpressure) is it going to flow more or less? Easy, less. If the cat flows into a restrictive Y pipe, resonator, silencer(s) kinked pipes, chambered muffler, obstructions, air damns, etc... each part adds up and the engine cannot exhale efficiently. Now, reducing backpressure is one component of a complex system and is in fact interdependent with the other variables. Velocity is very important. Heat, accoustics, aerodynamics, shape, volume and transitions are all important parts of the equation. To "simplify"... let me attempt to illustrate what happens in a multi-cylinder exhaust system. As an exhaust valve opens it "vents" the hot under pressure exhaust gases from the cylinder. These gases have mass and speed and therefore enertia. The speed is dependent upon many things not the least of which is heat energy. If you look at the outside bend of a header on an engine under load you will often see the "glow" of this energy being "lost" as it makes the transition. The purpose for ANY performance exhaust is to reduce the pressure at the exhaust port especially during the end of the exhaust event for that port. A really GOOD system can actually create a vacuum. This is called scavenging and it improves removal of unburnable exhaust gas from the cylinder allowing more fresh air/fuel charge to enter during the intake event as well as reducing the pumping loss of a piston working against port pressure. There are several ways to reduce this pressure including "tuned" length runners which "tune" the pressure waves to create the above effect... but only for a given RPM window. One of the MOST confusing realities about modifying exhaust systems is the usual loss of low RPM power/torque. Looking at a stock exhaust manifold or system logic would state that increasing capacity "HAS TO" increase flow and continuing this concept... POWER. So WHY would a better LOOKING part hurt low RPM power/torque? The answer is that the stock stuff flows POORLY both WAYS!!! Better flowing pipes flow better BOTH WAYS!!! When the exhaust event first starts (when the valve first opens) there is very high pressure in the chamber. This pressure flows out the POOR flowing manifolds just fine at low RPM. As the exhaust event is nearing its end the cylinder pressure is much lower and the poor flowing manifold acts to reduce reverse flow from other cylinders firing into the manifold. Installing a better flowing manifold CAN (not necessarily will) allow exhaust pressure from an adjacent port to flow back into a port at the end of its event and therefore charging that cylinder with additional exhaust pressure and reducing its potential to breath in a fresh charge. Think of it this way. With 4 exhaust ports collected into one exhaust manifold, if one of those ports is at the end of its exhaust event and has relatively low pressure AND one of the other ports is just starting its exh event and has very high pressure, the high pressure will try to back flow into the first port. This same idea applies to X and Y pipes. They act to create a high flow one way check valve that reduces reversion and therefore pressure before them. Properly designed they increase scavenging at low RPMs without restricting high RPM flow. This is why they help low RPM torque. This also applies to header merge collector theory/design With a large volume collector the gasses slow dramatically, pressure spikes and YES it can and does definitely flow backwards from the high pressure collector to the low pressure (relatively speaking) ports at the end of their exhaust event or at overlap. With a precision merge collector you can actually create a vacuum under the same conditions as the flow moves quickly through the small volume collector and "pulls" on the other primary. These conditions occur mostly at low to mid rpm and contribute to the old wives tale of an engine needing backpressure. Engines need vacuum in the exhaust! People think they need huge pipes but in fact large pipe is the biggest mistake made by most. Consider that the GS400 is rated 300hp/310tq and has a single 2.35" center pipe... and that my LS400 is rated 290hp/300tq and has a single 1.95" center pipe... it stands to reason that a single 2.25" pipe can support 300hp. So, using dual 2.25"s mean that you could support 600hp, not optimally but it would do it.' Ok, got all that?? I had to read it a couple of times too!!
-
Bump...
-
I can see that a lot of tuners would not see this as a major concern. They are aiming for a specific A/F ratio and the injector duty cycle is set to achieve that ratio. The fact that they loose the time/fuel taken to open and close the injectors is invisible to them and they compenste for the lag, without realising, by extending the duty cycle slightly. URAS, did your tuner say the lag compensation was simply added to extend the duty cycle, or added to the start time to bring the event forward to correct the timing issue?? Also, how does the load placed on the engine affect the lag time?? I would have thought an injector would take x amount of time to open regardless of load...
-
Yeah I agree, although I would go as far as - ANY backpressure (Turbo or NA) = BAD!!!!!!!!!!!!!!!!!!!!! A lot of the 'exhaust experts??' arn't quite up with the play yet...
-
How does 'back pressure' help performance...??
-
Hey Sydneykid That was a superb writeup with some excellent information... How does your principle/formula relate to internal wastegates and why do so many people have problems with them?? Can you predict internal gate performance/problems using this formula?? If a turbo is, as you said, near optimum for the boost and horsepower required (that is correctly sized for the application) and used at high boost levels at or near to it's potential, then it needs a smaller wastegate to control boost levels. Wouldn't an internal gate be able to control boost in this case?? Also you mentioned that an external wastegate with a flapper type valve flowed more than any of the poppet style valves. Does this also apply to internal gates as they are a flapper type?? If so, would an internal gate flow more than an equivalent size external gate?? See what happens when you make me think!! Cheers Bill
-
Thats true, abu... If you use synthetic oil from startup the rings will not bed in properly, it will glaze the bores and be an oil burner for the rest of it's life. Use a good quality mineral oil for the first 5000km and then change to synthetic...
-
Hi Only listing I could find was for the GTR... Upgrade time...? No two piece for the rear as the handbrake shoes use the inside of the hub, not good on an ally hub. Cheers
-
Any item sold should be 'fit for the intended purpose' It doesn't mater what it cost, if its a copy or the real mccoy or where it was purchased from... The plenum is faulty and the man deserves a repair or refund. Put yourselves in his position and I guarantee you would be the first to complain!!!