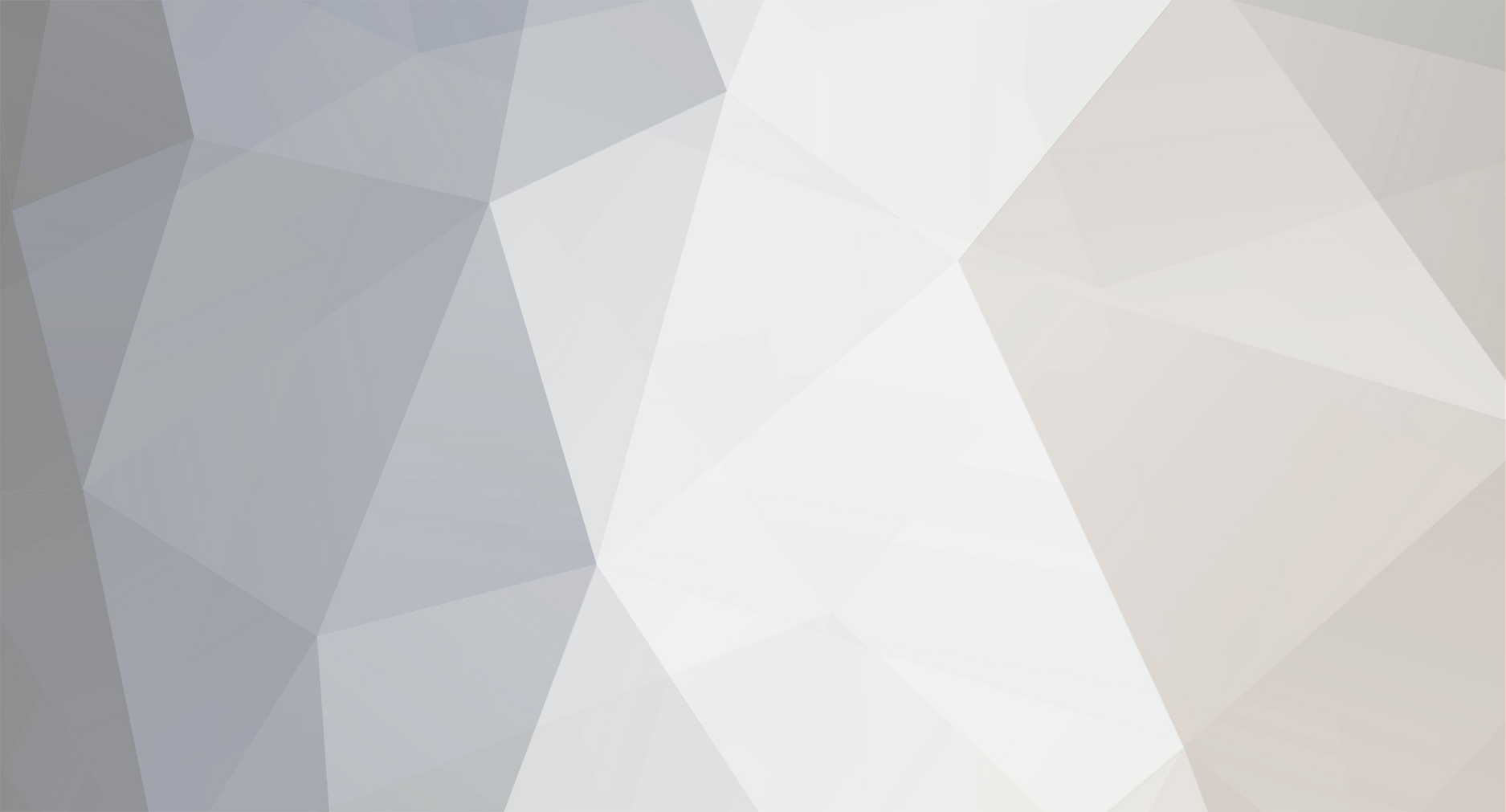
leeroy_25
Members-
Posts
169 -
Joined
-
Last visited
-
Feedback
0%
Content Type
Profiles
Forums
Events
Gallery
Media Demo
Store
Everything posted by leeroy_25
-
Okay.. So here is a screen dump of my current MAF table page: I would really really appreciate some advice on this.. I took me ages to get the table I have and the graph is very nice and smooth! I guess just all pretty much needs shifting down I assume? So I want to be sure I do it correctly and ideally would love some key figures I can plug in to guide me. Status.. really hoping you will be so kind. Could these MAF setup issues explain the AFR's globally dropping between 2 consecutive runs with no relevant map alteration? I am guessing not but just in case! If you look at my dyno post you will see what I mean! http://www.skylinesaustralia.com/forums/topic/370573-rb3026-final-tune-feedback/page__p__5910636__fromsearch__1#entry5910636 Thank you Lee
-
Thanks for the replies again guy's.. So Just to clarify as I think maybe some people have read the wrong graphs or lines of text.. At the mo I am at 437rwhp at around 6500rpm and 1.1bar (I say 1.1bar because it is not holding 1.2 yet! max torque at the wheels is 410ftlbs at 4500rpm ish. The 518bhp figure is estimate flywheel.. which I guess in turn gives around 460ftlbs at the flywheel? So, R31Nismoid.. you say laggy.. I can see your point looking at the plain numbers like that but it sure doesn't feel laggy! I thought the idea of a big engine was so you don't need to rely on the turbo so much! If it came on too much sooner I would go through tyres like no tomorrow! It spins up in third easy as it is! I have spoken to other guy's with similar rpm limit goals. ie 7000rpm and they are seeing similar boost response on Garrets and so on? I was hoping to get a bit in before maybe around 3500rpm would be nice. When you say a GT35 comes in a lot sooner when roughly? I would ideally have gone for a exhaust housing smaller but I could not find one at the time so had to take a flyer on this one! My build is on a very tight budget! and as they say beggars cannot be choosers! KiwiRS4T - that makes some sense also.. I think the Holset can run 3bar all day! But I won't try!! I do see how the other restrictions then come in to play. So, guy's I am really keen to get some thoughts on the reason the AFR's changed from one run to another like that with only a top end lean adjustment resulting in a richer map. It seemed to possibly get richer when doing runs in quick succession.. so maybe heat somewhere? air intake temps? I noticed on the road today cruising at around 50mph the intake temp is hitting around 40-42 degs? with a some speed up it drops to the high 30's.. Not sure if that is an issue.. undoubtedly it was probably hotter on the dyno with lack of air circulation. O2 sensors? I did wonder whether the pump was struggling and keeping up one run then not so well the next but as I said the injector duty seemed to be unaffected which I would have expected if the pump was an issue? The only other thing is line pressure if the in tank relief valve or what ever it is is causing a problem? I am also changing the filter just in case. Boost wise I will pre-load the spring and sort that out. I wanted to run a low setting or 0.8 bar really but I guess I can go up a bit on that and take the spring load as close to that as possible Exhaust wise does quiet always mean restrictive? I think the back box just bolts on at the tail If so I could run it on the dyno with the box off and see if that makes any difference? Please do keep the thoughts and ideas coming.. it is all helpful. Thank you Lee
-
Okay.. I guess that is a fair point.. but can I offer a counter.. Why can I not then run 2 or 3bar boost? I totally see where you are coming from but then there must be other factors as well otherwise no one would be running forged bottom ends and everyone would be on crazy levels of boost? I will see what happens when I can get it to hold 1.2bar boost properly and stop the fuelling problem.. I could tweak the cams back the other way to get more top end I guess but then I am just chasing big numbers and sacrificing where it counts? Thanks again Lee
-
Hi There, This very big table is what I have populated with my calculated numbers in the first place. So if I have say 80% in the global adjustment range for one voltage set do I just take 80% of the value of the figures in the table for that voltage range? Can you maybe give me a pointer a to what your chart starts at for Q45's and what it ends at just to give me an idea of where I am going? I can try and post a screen shot later. Thank you Lee
-
Thanks guy's E85?! I am running this as a road car so sticking to pump gas only I am afraid 99 octane! Injector wise I am getting 80% duty at the mo so still a bit of room there! IIRC E85 requires bigger injectors anyway so I assume that is why you mention that? Remember the dyno rpm scale is out so where it shows peak at around say 6250 it is actually 6500rpm real world.. Running it past that at present the power dips off. I could probably adjust the cams back a bit to up the peak power but then I will lose it in the low-mid range where it matters. Would be interested to see how that compares to other dyno print-outs at the mid range. KiwiRS4T.. Surely boost will kill a bottom end if you go too high? sure I understand it is all in the tune to an extent but surely more boost is physically more load on the pistons and rods and will bend or crack something eventually no matter how good the tune? Oh so the increase I have from 0.8 bar 370rwhp (rich map) to 1.1bar 440rwhp sounds about right? I say 1.1bar as that is where the boost is at peak power. On a slight side note can someone tell me if when I upgrade my in tank pump should have removed the in-line pressure regulator thing that connects above the pump in tank on the R33 GTR?? Not sure if that buggers up the flow on a larger pump? Also while on fuelling can you confirm if I am right in thinking the OEM FPR is good for 600bhp? i.e more than I am looking at? I just want to try and figure out the reason for the random AFR changes on the runs. It happened more than once. Could it be O2 sensors messing around? Thank you Lee
-
Cheers for the feedback guy's that makes me feel better! For some more info.. The Holset is an HX40 with 19cm housing so should be no problem for it.. if anything it is a touch on the large side! The manifold is XS Power tubular stainless top mount type with T4 flange. I have modified it with a large wastegate section to fit the 60mm gate and also beefed it up to hopefully stop it cracking at the joints! I did also tidy up inside as much as I could. A guy I spoke to actually implied the pipe diamter was a bit too large for optimal boost anyway? The rest of the system is 3.25" inch all the way back.. But I have to say other than the screamer pipe it is very quiet? I thought maybe due to the large turbo? I wil have yo check the make of the back box. I am running OEM intercooler.. I thought they are good for 600bhp? Also OEM FPR.. which I thought the same?? Another possibilty with the fueling is there was some kind of regulator or over pressure valve in the tank after the pump.. (R33 V-spec). Should I have taken this out as I left it in not being too sure of it's function? As you can see from the AFR's on the print out the car is no going too lean.. Still that is not to say the pump is struggling on one run and then keep up on the next giving extra line pressure? Not sure if that would account for the changes? I certainly don't want to run more boost than 1.2bar on my stock bottom end as I am kean that it be a good reliable daily driver! So hopefully I can make my goal by sorting out these few issues? Barring in mind I started out with 370rwhp on 0.8 bar and a rich map I also wondered if maybe the cam timing is restricting the high boost from being effective? I thought the boost increase would give more gain than that in itself? Having said that I did time the cams to give me optimum boost response and low-mid power which in reality is all you get to use 90% of the time! Please keep the feedback and thoughts coming. Thank you Lee
-
Hi Status, I have made a bit of progress tunning.. But not enough!.. Can you send me a pm of your e-mail address so I can drop you a mail. Thank you Lee
-
Okay guy's.. I have just had my final tune done on my RB30/26 and was hoping to get a bit of feedback on it and maybe some pointers to squeeze out a bit more bhp!. As ever we pushed for time at the tuners which was a shame as it could do with a bit more of a tickle. But I need to change a few bits as well so seems a good time to stop and get some other opinions!? Quick spec breakdown RB30/26 HKS264 step 1 cams Standard RB30 bottom end lightened and balanced rods Holset single turbo 60mm external wastegate 600cc injectors Bosch type intank in pump (Good UK made copy!) Stock intercooler Stock FPR Standard breather system setup rigged back into turbo inlet y-pipe after MAF's Q45 Twin MAF's Just to give a brief run down my previous tune 2 weeks ago resulted in 370 rwhp(440 flywheel power) on the stock MAF's. I then swapped on some Q45 MAF's and got the map back to the same results all barr a little running issue that was it sometimes stalled when lifting off from high rpm and putting it in neutral. There is a thread about that here: http://www.skylinesaustralia.com/forums/topic/369343-q45-maf-pointer/page__p__5891148__fromsearch__1#entry5891148 So this weekend we proceeded as follows. The tuner leaned out the map a bit at the top end and altered some of the MAF settings to try and cure the stalling issue. It is better but not perfect for sure. I also found out my Stock oil breather system setup was leaking through both one way valves! So even though it's a closed system I expect that won't be helping anything, especially when it's on boost! Anyway, we stepped up the boost to 1.0bar and then 1.1bar and finally 1.2bar and the results are as follows: So just under 440bhp at the rear wheels and that was 6500rpm. (dyno rpm scale is out a bit) We opened up the rev limit a touch and you can see it starts to fall off the power after around 6600 anyway. Also the boost starts tailing back off to 1.1bar at the top end? It held 1.0 bar fine and 1.1 pretty well.. bt 1.2 it's struggling. maybe boost controller setup or the 10psi wastegate spring is not man enough? But in any case this is where I wanted it to make power as the low down power is what you can really use! I must say I was hoping to hit just over 450bhp to be close on 550bhp flywheel power. Maybe with some tweaks it can get there? This is where I would like some thoughts as to waht might be limiting me? Stock intercooler? Stock Fuel reg? exhaust? You will see something a bit odd if you take note of the two runs shown...both runs were done one after the other with a minor top end tweak on the fuel map to lean it out but yet the second run the AFR map has jumped down (richer) over a significant portion of the run??? Anyone got any ideas what could cause this? I was wondering fuel pump running in tank bosch type with the Inline in tank pressure regulator still fitted? I have no gauge on it to check pressure at present? But that said I would have thought that would only really effect the very top end and the injector duty would go up which it didn't? Also it makes pretty much the same power?! Could it be MAF related again, plugs or coils? The leaking one way valves on the breather system? Some ideas on this would help please if anyone has a thought! I am running the stock FPR for info. But was told ages ago that should be fine for what I am aiming at? Boost wise I am going to check the settings on my boost controller and also put a bit of pre-tension on the wastegate spring to try and hold it better up top. Anyway.. Let me know your general thoughts! I am happy but not ecstatic! Cheers Lee
-
Email Notifications Not Working?
leeroy_25 replied to NewKleer's topic in Site discussion - including Ideas/Feedback & Bugs
Thanks for info. Firstly I checked my junk straight away to check this. No mails there. I have noticed the odd mail for new topics being started in one of the forums which think I opted for a while ago. but I don't get them as often as I used to. Also to clarify the e-mail notification box is ticked automatically hen I make a post or reply as that is what I set my control panel to. I just made a habit of checking it was for sure recently when I stopped getting e-mails! I cannot really unsubscribe from watched topics as I am watching a lot and some are for a very good reason and I may not find them again if I unsubscribe. I guess I could try unsubscribing from some I don't need any more and see if that helps? Maybe there is a subscription limit we are not aware of?! Cheers Lee -
You say that but the Q45 on an RB25 is only running 1 MAF. If you look at the values for the other options on the RB25 Like the VG30 you will note that the numbers are different to the ones in the RB26 VG30 option. So to let out my secret! I basically found the common scaling factor between the common MAF's in the RB25 and RB26 datalogit tables and then worked out the Q45 MAF table from that. Maybe my scale is wrong so all my numbers are out an amount? Maybe the scaling is not linear in that way from RB25 to RB26.. It did seem to work on the other checks I made? Maybe I should post up a screen dump of the MAF table from my datalogit screen for discussion? If I understand you correctly you thin that if for instance I have had to use a % value of 80% in the voltage boxes I need to make that 100% again and then scale every different voltage cell in the MAF table by the appropriate %? Can you please clarify how this is different to using the global voltage scaling? Does that have an impact on something else? I must say I drove the car today and it is way smoother than it ever was on the Stock MAF's! I have not managed to stall it driving yet as like I said before you don't tend to just put your foot on the clutch from high rpm! You only really notice something is not quite right when you change gear slow giving the revs a chance to die right down. Grateful for the advise by the way guy's.. Thank you Lee
-
Email Notifications Not Working?
leeroy_25 replied to NewKleer's topic in Site discussion - including Ideas/Feedback & Bugs
Err yes!! I have checked all settings and checked that box is ticked every time I make a post.. Still no joy though? By the way I did not get a notification for this post.. Just came on to check by chance. Lee -
Email Notifications Not Working?
leeroy_25 replied to NewKleer's topic in Site discussion - including Ideas/Feedback & Bugs
Hi There, I have not been getting e-mail notifications to subscribed threads and posts for a while now. Checked all my settings and they seem fine. Please can you let me know if this can be resolved. Thank you Lee -
Thanks for the info guy's.. I will try and get a copy of my MAF for starters. Just to clairfy I am not running a BOV? So I assume this reversion you mention is air trying to blow back out of the MAF when you lift off and the turbo slows? Would fitting a BOV improve the situation? I am not sure what you mean Status for why not to use the global adjustments? I assumed these just shift the MAF graph up or down accordingly? Are you saying in fact the MAF readings should remain at 100% and the fuel map would need adjusting accordingly? I can see pro's and cons' either way. Assuming the fueling was correct on the Standard MAF's which it was I would imagine the adjustment would be needed on the MAF table to bring it all back into alignment or closer at least. Then fine tune the fuel map? I am not tuner don't get me wrong.. Just would like to learn the exact reasons why not to do something one way for my own knowledge. Thank you Lee
-
Okay.. despite all the bad press I decided to give my Q45's a go on my RB26/30 build as I had them ready with piping wiring and the lot. So by some trickery I worked out a way to calculate the required data to put in my RB26 Apexi MAF setup to suit the Q45's! I must say to my surprise when I put them on a turned the key it fired up and idled beautifully.. Even seemed to rev cleanly. So After my trip to the dyno for a quick map and play we did some testing. I started with the stock MAF's ran it up and got a happy map.. Then I put on the Q45's. All was good other than they globally seemed to shift the fuelling quite a bit and make the entire map hugely rich! My Tuner then showed me that we could get around this using the % values against the voltages in the MAF setup screen. This seemed to do the trick. Now after all done and running up basically fine. The only slight complaint I have is when we did a pull on the dyno and then lift of the throttle and pop it in neutral the engine revs drop and it stalls! You can catch it with a light rev back up. It's fine on the road as it is rear you rev it and then dip the clutch like that.. but it does get close sometimes! Has anyone got any ideas on how to get around this?? Maybe the voltage % values need adjusting back up in this area only as they are effecting the MAF effectiveness/resolution?? Also I have noticed that if you really jam the throttle quick it can hiccup a bit. but that also is not likely to happen in normal use and may not be related to the MAF's. Alternatively could be the same cause as above? Any advise would be good as I am so close to having these working just fine it would appear! Thank you Lee _____
-
Cam Timing Using Lift In Mm At Tdc Method
leeroy_25 replied to leeroy_25's topic in Engines & Forced Induction
Thanks for the reply.. I have some info also from HKS about the duration of the cams at 1mm.. From this I could roughly say the for instance the exhaust cam should be just under 1mm open at TDC. When My cam pulley was set to 0 I had nearly 2mm lift at this point! I had similar on the inlet cam but again going by the 1mm valve lift info from HKS the valve would be just over a mm at TDC? It appears looking at my cam pulleys that the exhaust cam sits about half tooth out anyway? is this common with RB30 conversions? Maybe the belts have a slightly different pitch? Or maybe my eyes are just out! As it is I will go an play with it on a dyno tomorrow and dial it back towards the zero marks and see what I get. I presume to get a valve and piston collision on stock lift or very mild cams the cam timing would have to be further out that the possible adjustment? I.e a couple or teeth? What about valve to valve collision? Is that possible? Cheers Lee -
Can anyone who uses the mm lift at TDC method for cam timing please reply here or better still pm as I dont seem to be getting any notifications at the moment! I would really like a couple of points about a general base setup and maximum difference between inlet and exhaust lift to avoid collisions. Thank you Lee
-
Rb30/26 Hks Step 1 Cam Timing Please Help
leeroy_25 replied to leeroy_25's topic in Engines & Forced Induction
Come one guys' some one surely can shed a bit of light on this?? Even if you can give me base settings for another mild aftermarket cam or standard Nissan ones that would probably give me a pretty good idea as to what I am working with.. Just need the factory base setting for mm of lift at TDC (non-firing) for each cam please. Thank you Lee -
Rb30/26 Hks Step 1 Cam Timing Please Help
leeroy_25 replied to leeroy_25's topic in Engines & Forced Induction
Hi Rob, Just to be sure I was working this correctly in my head.. if I started with 2.1lift inlet and 1.9 lift exhaust you have suggested I Advance the inlet a touch to 2.2mm lift which is the opposite to what I have done so far but makes sense with what I have read before. With the exhaust I need to advance it also on my standard lift measurement to 0.8mm? I have to say I am not convinced the pulley aligns correctly with the timing mark on the back plate for the exhaust side so this may be out to start with? As I said I have not reference as to what '0' marks would normally relate to lift wise for the cams? As I have read normally the exhaust timing is retarded to increase spool up? This would laso lead me to believe my start point is incorrect. So in fact the measurements you have stated are not a million miles out fomr what i have. I actually set my exhaust to aout 0.9mm in the end when I did it as it seemed a hugh adjustment in degrees!? I don't envisage back pressure being an issue as I have quite a large turbo and downpipe! I presume I can monitor this with EGT's? If you can give me an idea what mm@TDC settings would normally be on zero that woul dbe great.. I am wondering if there is a slight difference in my inlet and exhaust cam pullies that I did not notice and have them on back to front? I guess it does not matter much if they are adjusted right now? Cheers Lee -
Hi Guy's I am really hoping someone can give me some help here or eve a few peoples opinions so I can get an average! I recently finished putting my engine back together. While doing so I thought I would time my cams (HKS Step1 264) using the lift at TDC method. I am running a Holset turbo which can work with slightly different timing to a garret type turbo but the overall picture should be roughly the same. I was given some timing to try by a tuner in Europe who has supplied a lot of Holset turbo's for various builds. He aid try 1.3mm lift @ TDC for inlet and 0.7mm Lift for exhaust. I initially had my pullies set at 0deg when it went back together although I do not know how accurate this is to the stock lift setting recommendation. For a start I cannot find a listing for HKS cams in mm @TDC? Anyway 0degs on the pullies equated to about 2.1mm lift Inlet and 1.9mm lift exhaust. After adjusting as suggested It gives an equivalent adjustment of 8deg Inlet (retarded is that right?) and 10degs Exhaust (advanced?).. I thought this was excessive so dropped the exhaust back to about 8degs also. Anyway.. As recommended this should bring my boost on lower? Also note I am trying to bring the power band lower down a I am running a stock RB30 bottom end and revving to 7000 redline. I believe this adjustment is pretty much opposite to normal? Anyway.. previously before adjusting I would make my boost by 4250rpm.. Now it seems I am around 5000rpm t reach the same boost with no other changes?! So clearly something is not quite right with my recommended adjustment or I have done something wrong? Please let me know your thoughts guy's so I can get this somewhere near right prior to going to the dyno! Cheers Lee P.S. Can someone help with e-mail notifications? I am not getting them any more but all my notification settings are on! And I have checked my junk too! Thank you Lee
-
Well that's nice and easy! I could just go with that and be one with it.. Although I think I will take both breather to a bottle and leave it at that. Just got to try and turn the fittings in the cam cover around to suit. And out what thread I need to block the PCV. Cheers Lee
-
Arhh.. I can only just see it I think in that picture. You mean the hole on the fitting in the cam cover needs blanking? I have RB26 covers so slightly different. I can connect the two covers together and no need to blank anything but I would need to blank of the fitting on top of the throttle body back plate where the RB26 inlet cover connects to. On a side note anyone know how to contact admin? I don't seem to be getting notification e-mails any more.. I only checked in by chance the last couple of times!? Cheers Lee
-
Thank you so much for the replies guy's there are so man opinions on this it is hard to know which way to go. I am all for simple as long as it's effective.. All sorts of fancy setups have been suggested with vents to the downpipe to draw fumes etc.. All very nice but I was thinking overkill for my street car. Now I like your setup 3BEPKA. Do you not have a vent or connection to the bottom end at all? It looks very much like a RIPs setup? I have to say I thought the pressure in the sump would be the main cause of breathing issues as like Dale says I guess this is working against the oil trying to drain back from the head to the sump normally? So having a vent for the sump should be a good mod? I guess the argument is it is not there on the standard setup!? I like the idea of having a t-piece into my head-sump line that goes to the top of the breather as well so I can get the sump breathing through this but oil can still try and drain from the head back this was if needed. I guess if it did turn out to breath a lot (hopefully note!) I could then add another t-joint to allow the catch tank to be drained back to the sump via a valve.. but this is starting to get a bit messy in pipework! just to be clear I don't think I have a breathing issue.. I had a small bit of oil blow/get sucked out once after a hard run.. Then someone looked at the breather setup I had and said I should really have it setup to a catch bottle anyway! So the PCV that needs blocking off I assume is the one that goes in behind the throttle plates. At a guess the fitting in there unscrews and you can blank it with an M10 bolt? or whatever thread size it is? Dale you also mention improving the screens in the cam covers? please explain more. I am not sure what you mean by this or how to do so? The baffles in the top of the cam covers have some kind of foam filter behind them from memory. Lastly the connections for the breather pipes in the top of an r26 cam cover.. can these be turned around or removed easily? I either would like it so the spouts to connect the covers together face each other leaving the other spouts facing forward towards my catch tank or remove them completely and replace with some nice 90deg fittings. Thank you Lee
-
Does anyone know the standard/recommended lift at TDC setting for HKS step 1 264 cams please? Ideally I would like a base for my adjustments! Thank you Lee
-
Okay. I am specifically working on an RB30/RB26 combo but I guess the question applies across the board hence I have posted it here. I have currently got my breather setup similar to a factory setup. I am converted to a large single turbo and have the exhaust cam cover breathing to the turbo inlet and the inlet cam cover venting behind the throttle bodies as standard. In addition I have a breather/drain connected from the back of the head to the sump high up as possible. I want to do away with this set-up under recommendation from a few people and run a simple catch tank setup.. The car is road used not a track car if this helps. My plan was to run the cam cover breathers to the top of a catch bottle and then I would have liked to run 2 from the sump to the bottle. One high as a breather and one low as a drain. But as I only have the option to run one from the sump I was thinking about putting a t piece into the pipe running between the head and sump as close to the sump as possible and running this to the bottom of the bottle so if there is oil coming in to the bottle it can drain out and any major pressure could blow back up it? Please let me know your thoughts on this set-up. The catch tank would of course be vented with a filter. Thank you Lee
-
Hi There, Please can someone give me a pointer on this one? Cheers Lee