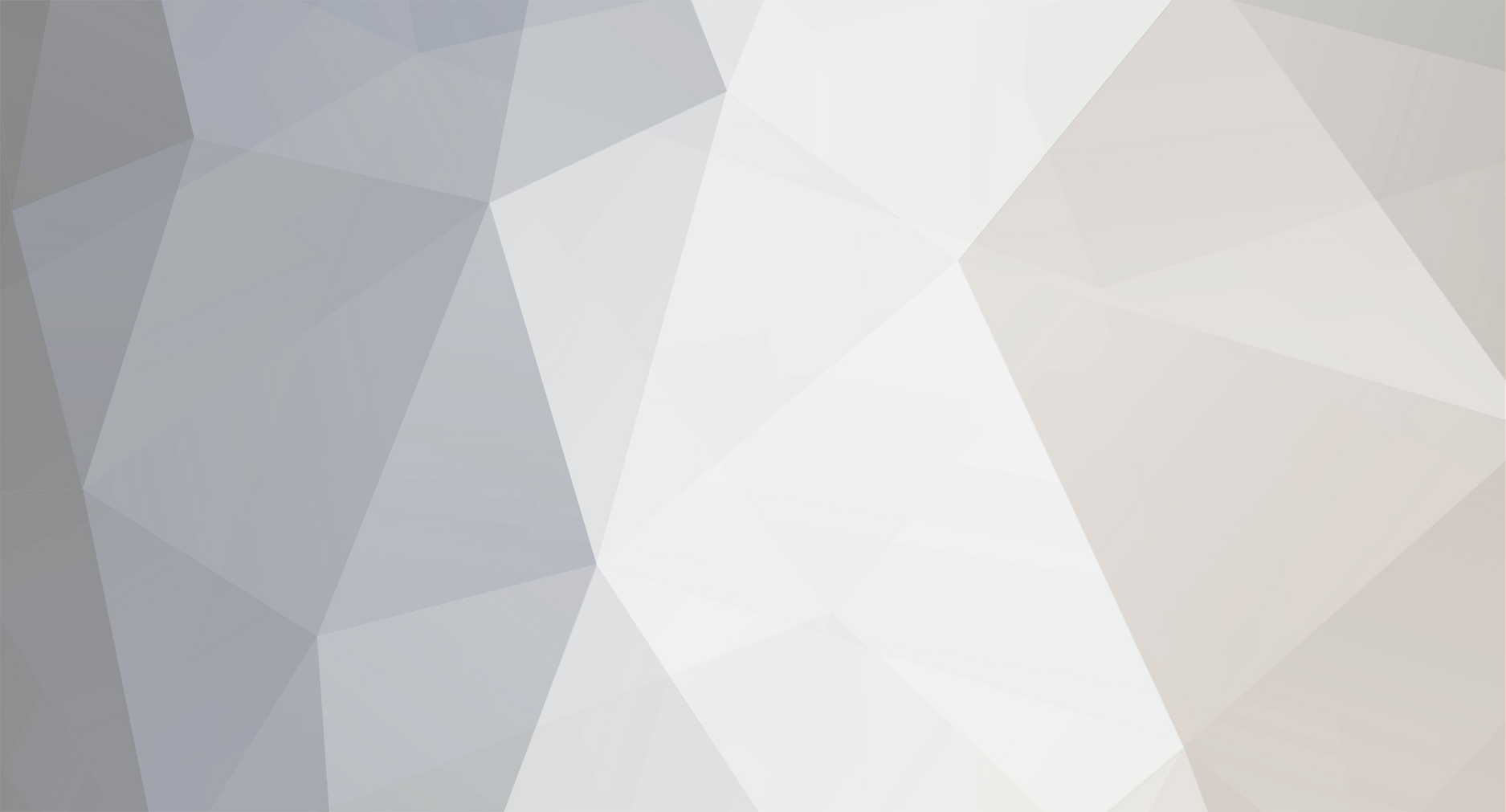
shaund
Members-
Posts
93 -
Joined
-
Last visited
-
Feedback
0%
Content Type
Profiles
Forums
Events
Gallery
Media Demo
Store
Everything posted by shaund
-
Oil/Coolant substance in Engine Harness
shaund replied to Carbonsky's topic in RB Series - R31, R32, R33, R34 (1986-2002)
if the liquid is conductive, it could be part of your alternator problem if its short circuiting anything... you may have to do your best to clean the harness and inspect for damage... if its just engine oil or PS fluid, you're probably fine... if you've had water/coolant in there, it'll probably be ok once its dried out so long as its not corroded through or caused any bad joints/connections. If your harness is really bad, you can probably get a section from a wrecker or (or maybe wiring specialties?) and patch it in upstream of where the damage is, or just replace the harness. Have a look at wiring specialities and see if they sell a replacement section for that area of the harness if you have to go down that road.. brand new high quality is a good way to go if you end up replacing parts of the harness. If you have to cut the harness and re-join a new bit on, add your own connector to make it a removable section. IMHO the harness really could have done with a few more connectors for modularity from the factory.- 3 replies
-
- engine
- engine harness
-
(and 5 more)
Tagged with:
-
My 91 Gtr R32 stutters and it has stalled..
shaund replied to Jcmz's topic in RB Series - R31, R32, R33, R34 (1986-2002)
Its very likely electrical... have a close look at the wiring harness.. specifically have a look at things like the part of the loom for the coils... that sits in a very hot area and over the ~20 years its been there, has been subject to allot of heat that will have caused the insulation to degrade.. its not uncommon for intermittent short circuits to occur here. If you need a replacement for the coil pack look, have a look at wiring specialties in the US.. buy direct... I looked at some cheaper stuff on ebay a while ago that claimed to be made by them, but it was likely a knockoff. When the problem occurs next, pay close attention to what you were doing at the time when it happened. Try to reproduce it by taking the same action (ie, turn right at speed, hit a speedbump at a particular speed, etc) - this might give some insight into what the cause is. -
I tend to not trust the volt meters in distribution blocks like that... I'd double check with a decent multimeter (something good like a fluke or a higher-end affordable brand is fine too)... As suggested by @Steve85, a drawing would be good.. so far your description sounds like you've done the right things though... If we make the assumption that the 18v you're seeing on the distribution block's meter isn't false, Its possible in your re-wiring that you've somehow dropped the voltage sense line from the alternator, and the alternator is just outputting maximum voltage based on RPM. Most alternators will have 3 basic connections. Ground, Charge, and Voltage Sense. Ground goes to the body, Charge is a big fat wire that goes to the battery to charge it, and the Voltage Sense line is a skinny wire that should go directly to the battery to sense voltage at the battery. This allows the alternator to adjust is voltage regulation up when the electrical system in the car is under heavy load, or if the battery is flat, to make sure voltage is regulated at the battery. Have a look in the workshop manual and see if you can find the part of the wiring diagram that deals with the voltage sense line, and identify it on the plug on the alternator. measure voltage with a multimeter between that pin on the harness and the negative terminal on the battery - you should see +12V. As an extra diagnostic, assuming your battery is good, you could disconnect your alternator completely from the car electrical system (be careful to insulate the big charge lead at the alternator side) and run the car without the alternator. If it starts, runs, behaves normally, and you don't see the voltage spike, it may be alternator or alternator wiring related.
-
the only thing that'll cause a fuse to blow is a short circuit or faulty equipment... I'm not sure how you'd manage to 'smoke' your radio... did you some how reverse the polarity to it? The way I wired mine was (and this is not a guide or how-to, no warranty, seek professional help, blah blah) After mounting the new batteries and removing the old one: 1. Cut down the battery ground strap to remove the excess length and thereby the negative terminal that normally bolts to the battery (car body is your ground). 2. Make an electrically sound new ground for the battery in the boot. 3. Install a postive cable from new battery in boot (with appropriate fuse/isolator in the boot) to the front of the car 4. Join via a busbar onto the original battery positive terminal. This is installed inside a well insulated box that is hard mounted in the engine bay. I maintained the original fuse box, fusible links etc in the engine bay - I saw no need to change this - it didn't need improving. Its critical to remember that there is enough stored energy in your car battery to create a fire very quickly. If you're improperly fused and you get a short circuit, there is a potential to set your car on fire. Electricity often doesn't get the respect it deserves. With a single average car battery you often have a fault current (short circuit) in the region of 1000A. looking at how your power distribution block is mounted to the body in the engine bay, it looks like its just got a thin sheet of plastic as insulation between it and the body (ground). I'd be re-thinking it a bit to see if some more insulation can be added - a piece of thick strong plastic as part of the mount, and/or or a decent thick plastic box to enclose it. Do you have a fuse at the battery end? What size is it? My intention is not to be insulting or unhelpful, but If you're not 100% certain of what you're doing, at the very least seek the advice of a competent auto/commercial electrician, or electrical engineer. It'll be cheaper than replacing a car that gets burnt to the ground by an electrical fault. Cheers!
-
I made up an aluminium plate with rubber glued on the top for the batteries to sit on. Under this, I have 2x steel straps with holes that bolt through the floor, and then allow some threaded rod to extend upwards to another steel strap on top of each battery. For the bolting to the floor, I used painted steel plates underneath the car to re-inforce, and stainless fastners, loaded up with black sickaflex sealant. The bolts go through the aluminium plate, through the metal straps, through the floor, through the re-inforcement plate underneath and then nuts with lock washers bolt it rigidly to the body. Getting the re-inrforcement plate under the floor and getting it all bolted up was really difficult... It'd be easy if the rear subframe and/or diff was out... but its doable without removing anything from underneath if you have a second person on top to do up the bolts for you. The idea of welding a bracket to the strut tower brace is neat.. should be solid enough too. I think thats good for an "easy bolt-on", but I don't see it as a big deal to bolt through the floor if you goto the effort to make sure its sealed and rust proofed. You also probably don't need to use two batteries of the size I used. I've seen some dedicated track cars that use a single battery half the size of one of mine.
-
I ended up putting in 2x HC35s in parallel, and used an ANL fuse holder with 250A fuse because my 300A stinger breakers were lost in the mail. I fabricated an aluminium panel for a giant on/off switch, the ANL holder and a small fused distribution block for things like fuel pump and stereo. To hide it all away I fabricated a wooden panel covered in matching fabric and some metal brackets to cover it over to hide it away. I'm pretty pleased with the result. Battery spec sheet: http://www.fullriver.com/products/admin/upfile/HC35.pdf Fuse Holder: https://www.jaycar.com.au/anl-in-line-fuse-holder/p/SZ2078
-
rb26 inlet valve stem discolouration/damage?
shaund replied to shaund's topic in Forced Induction Performance
Thanks... Nah, they look pretty much as per the photo... there is a bit of a shadow, but its not making things look any worse than it really is. I'll try to get some better photos on the weekend... I want to have a good look at the rest of the valve stems for both inlet and exhaust. Cheers! -Shaun -
rb26 inlet valve stem discolouration/damage? Hi All, I've just removed my inlet manifold to have it painted and noticed that the two inlet valves in cyl 3 have some discolouration on the valve stems immediately below the valve guides. Is this normal, or should I be looking at replacing valves, guides, and seals? This is an R33 GTR motor that is stock (except for cams and a little extra boost) and in otherwise good order and showing nothing as wrong in its performance or behaviour. I've yet to turn the motor over and inspect the rest of the valves when they are extended. Motor is at TDC on cyl1, so these are the only inlet valves extended. Photo is here: http://imgur.com/ZcPIgmp Cheers! -Shaun
-
There is a thread on gtr.co.uk with some detail.. I'm about to do the same on mine.. I got 300A stinger breakers. I'm running 35mm^2 cable from the battery in the boot up to the front and will be attaching it where the battery was originally connected. Do volt drop calcs for the length and size of cable you plan to run, remembering peak current draw on starter motor could be 200-300A, when its first breaking free. this should drop rapidly to somewhere in the region of about 150A. Use a drycell fully sealed battery. I got a fullriver HC35 for $200 from a local battery supplier - this will fit on its side under the rear strut tower brace. Good luck!
-
If there is a translated version kicking around, I'd be keen for a link too! The only one I've seen is a japanese language version. Cheers!
-
I just did an install in my Series 2 C34... Standard 6.5" all around. Used these speakers - http://www.german-maestro.de/US/cs6508.htm I put splits in the front - tweeters went into the factory A pillar positions and it was quite easy and totally hidden. Just make sure the tweeters are as close to the factory position as possible. While they are a bit thicker than the standard ones, the clips on the grill just clear the tweeter and it all fits up quite nicely. I connected them to the 0db point on the crossover and it sounds pretty balanced and linear. I used a bench grinder to modify the bracket for clearance and some hot glue to glue the new tweeter into the bracket, then it all just clipped in as factory. I also had to make a 19mm MDF spacer to bolt the new driver into the door.
-
Duncan: www.dropbox.com and then share the link from there.
-
I would translate bits as you say, but still have yet to find a WGNC34 manual. Not all of us have M35s you see
-
Hmm.. I signed up ages ago with these guys before they had the numbers... I was never email'd with what you have received.. I just hit up their contact form again... I seriously hope they get this done for us! Cheers! -Shaun
-
a C34 stagea manual would be very handy.. translated or not... good for torque figures and diagrams at the least... anyone who's got a copy able to share it via some method? Dropbox perhaps? My missus can read a little japanese and could potentially help with translating bits... big ask to do a whole manual, but on an as needed basis for something small may be doable.
-
Hi, If your getting no fault codes from the ECU for TPS, but a fault code from gearbox diagnostic, I'd guess that the TPS signal to the gearbox isn't getting there, or is dodgy. Its possible you've got a damaged wire, plug or socket somewhere along the way. This may have been damaged with the engine failure you've had and easily with the remove/install of the replacement engine. Its easy to stretch/crush wires in a wiring harness when you're hauling the engine in/out. Without seeing the wiring diagrams/manual, I'd guess that the TPS signal to the gearbox would be used to help figure out when to kickdown, and how long to hold gears under different levels of throttle. In the old days it used to be done with vacuum. Check the workshop manual for the skyline with the same engine as yours and look for the expected signal from the TPS and measure to confirm. I'd suggest measuring this at the TPS, and at the pin on the ECU to confirm good signal, and then see if you can find where the gearbox computer is, the pinout for it, and then confirm the signal there too. To measure signal at the ECU, use a fine piece of wire and shove it into the back of the ecu connector, following the wire. If you get lucky you'll make contact with the bare end of the crimp connector. Alternatively, you can use a sewing pin and puncture through the insulation of the wire near the ECU plug and use a crocodile clip on your multimeter to attach. A small dab of a rubbery glue over the pinhole is a good way to re-seal the insulation of the wire if you feel its necessary. Good luck!
-
Hardrace Front Upper Control Arms?
shaund replied to Sports Crazy's topic in Suspension, braking and tyres
they looks pretty good... I just ordered these myself: http://www.amsmotorsports.com/shop/ind/skyline/suspension/ams-adjustable-front-upper-control-arms.html -
Assuming you've not got issues with timing or bent valves, it may be just a very tired motor with rings that are badly worn. Other than low compression, are there any other symptoms or problems noises? coolant in the oil? oil in the coolant? lots of moisture/water coming out the exhaust? If you lift the oil filler cap is there milky crap on the underside? If its a reasonably stock engine, go for a wrecker motor. It may not be worth rebuilding. RB20 wrecker motors are cheap. its probably a good opportunity to do an RB25DET conversion.
-
So Standard oil pump should be fine until I get around to rebuilding then. I'm thinking about replacing it with a Nitto anyway, but concerned I may end up with over-oiling problems considering im not going to be taking the head off and installing any flow restrictors. Thanks for all the info guys... very helpful. Much appreciated! Cheers! -Shaun
-
Rb25 Air Flow Meters
shaund replied to zachscalais's topic in For Sale (Private Car Parts and Accessories)
Sold to me already. -
Hi Guys, Hoping some knowledgeable people would be happy to help me out with some advice... I'm wanting to upgrade my turbos from standard to -5s. I've been slowly working towards doing all the supporting mods without opening the engine... So far: - 3 In turbo back exhaust (Came with the car) - Nistune - Greddy Profect B Spec 2 - Bosch 044 - Power Enterprise 700cc Injectors - Tomei Poncam B's + Adjustable cam gears - Extended baffled sump + drain from rear of head (to go on at same time as turbos) - 2x RB25DET S1 AFMs (on their way - just picked 2 up cheap) - will probably upgrade to nismo/Z32s later if required. - Oil Filter relocation and cooler kit (Does wonders on the track for oil temps :DD ) This engine has a standard oil pump, but a late model/r33 crank with the longer engagement with the inner pump gear. To Aid tuning and for peace of mind I've added a wideband sensor+dash gauge, oil and fuel pressure sensors, all that come back to a DLP-IO8G board for logging in Nistune. I see good solid fuel and oil pressure. I've got a J&S Safeguard on the way too, that I should have in 2 weeks, and a big radiator to fit this weekend too - not strictly supporting mods though, but helpful none the less. I realise having an otherwise standard bottom end isn't ideal, but I intend to rebuild my spare engine and then transfer all the bolt-ons across later. Questions: 1- Is there anything else required to support the bigger turbos and make reliable power? 2- Do I need to do anything to regulate the oil flow to -5 turbos? Will i need to restrict flow to the turbos? Will the standard pump provide enough flow and pressure? 3- I've seen people talk about HKS actuators on the -5s before - what reason would you change the standard actuators to HKS? 4- Exhaust manifolds - I was thinking about just port matching the standard manifolds, or is there enough of a gain to warrant the expense of something like the Tomei Expreme manifolds? I'm still looking for somewhere to buy the turbos,gaskets,bolts/studs etc, so happy to take recommendations I do all the work myself including tuning - just want to make sure I've got everything covered before ripping the engine out and starting Cheers! -Shaun
-
Diagnosis Rb: Wha'ts The %#^$Ing Problem?
shaund replied to Cowboy1600's topic in Forced Induction Performance
Don't pull your injectors out. It won't tell you anything useful. The injectors are held into the inlet manifold by the fuel rail. If you undo it, you'll be up for a set of new O rings, and you'll end up with fuel pissing out everywhere, and a potential fire. If you want to check the CAS, mark its alignment against the tming cover housing, undo the bolts holding it in, and pull it out. Put the key to the "ON" position, and spin the CAS shaft by hand. You should hear the injectors fire (ticking noise as you do it), and in theory the plugs should fire. To test the plugs for spark, pull the coil packs off the plug, keep them connected to the wiring harness and shove a length of wire up into the coilpack where the sparkplug normally seats. With a friend helping you, get the other end of the wire near the block (but not touching) - within 0.5cm should be close enough, and spin the cas. See if you have spark. Be aware, you may get a jolt from the coil pack doing this if you're not careful. Good luck and be wary of keyboard mechanics giving you bad advice and telling you to do the wrong thing. Several people offering advice and suggestions who obviously have never done anything beyond an oil and filter change before! Bullshit filter to maximum! -
Based only on those photos, I'd say its just a rocker cover gasket leak, and/or half moon seal leak. Not a big deal to replace if thats all it is. New seals from Mr Nissan, a tiny bit of blue silicone for the 1/2 moons, and about 30-40 mins of work.