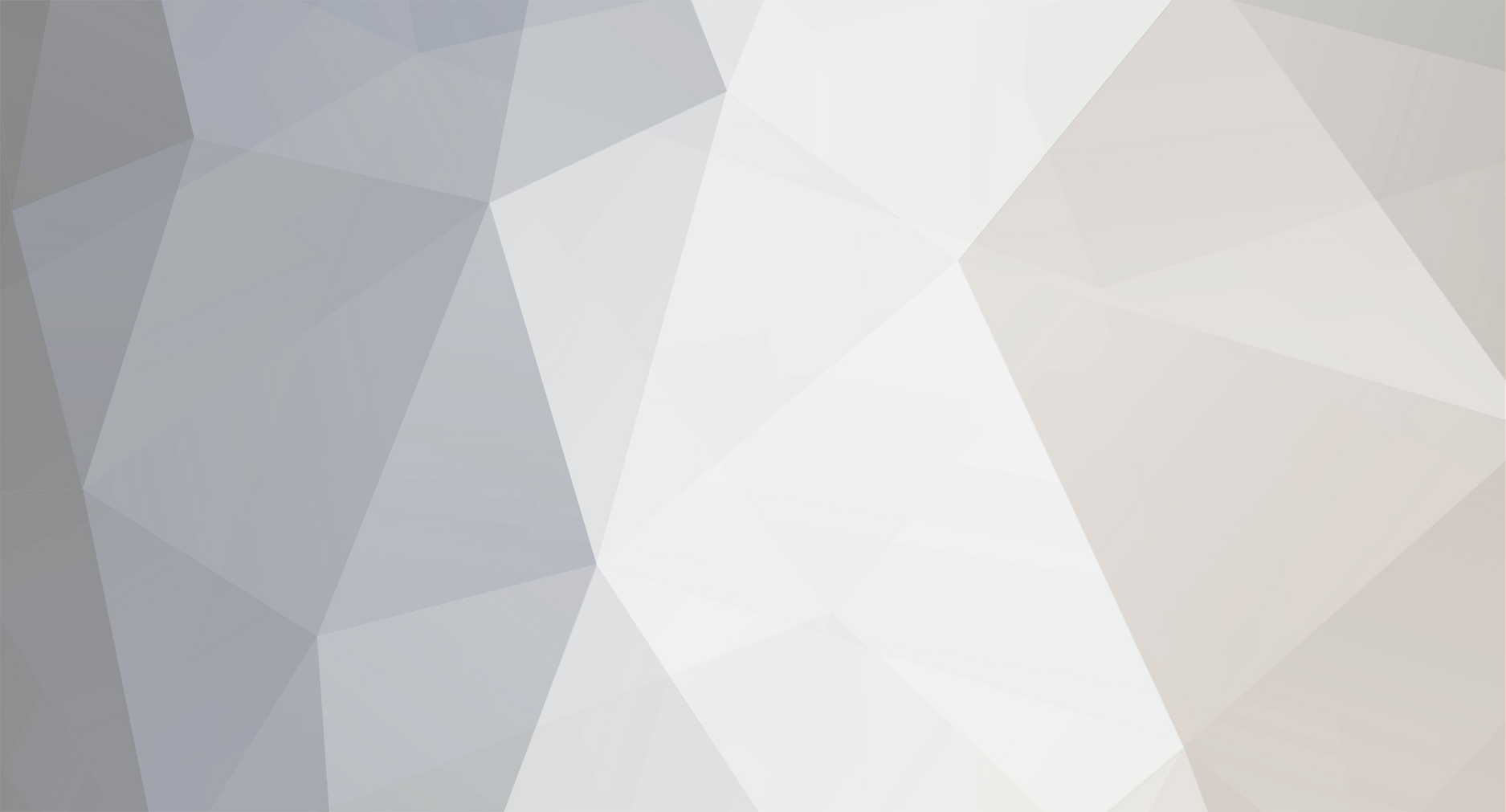
Dale FZ1
Members-
Posts
2,146 -
Joined
-
Last visited
-
Days Won
4 -
Feedback
100%
Dale FZ1 last won the day on October 24 2020
Dale FZ1 had the most liked content!
About Dale FZ1
- Birthday 29/10/1968
Contact Methods
-
Website URL
http://
Profile Information
-
Location
Sunshine Coast
Profile Fields
-
Car(s)
ECR33 Series 1
Recent Profile Visitors
9,470 profile views
Dale FZ1's Achievements
-
Great result, shows how much the element of persistence is part of getting to the top. Well done!
-
Mount Morgan, near Rockhampton.
-
Do you have either the parts numbers, or critical dimensions for that particular bearing? Can't imagine it hasn't been done before, and there's a few reputable bearing suppliers between Warwick, Toowoomba and Brisbane.
-
GTX3076R GEN II VS GTX3576R GEN II on RB26
Dale FZ1 replied to joe89's topic in Forced Induction Performance
I rejected split pulse/twin gate for generally similar reasons. Mainly because everything gets so busy and so hot. A properly thought out and executed divided pipe to a 60mm gate is what I'd consider if split pulse was chosen as "the next step". Truth (for me) is that there's too many other areas requiring priority consideration if you want to make the combination faster. The next step (for me) is to make the driver faster... Generally, the GTX3576 makes a lot of sense for tractability and a wide useable torque range regardless of whether single or split -
Get serious with current chassis or upgrade to something newer?
Dale FZ1 replied to robbo_rb180's topic in Motorsport
Agreed. Unlikely that Roger Penske will be contacting any SAU people to come drive for him anytime soon, and even WTAC have regs. I find that while my 33 requires $$ and effort to prepare and run, it's the enjoyment of actually running it that makes it feel worthwhile. There's a whole lot of sense to consider running budget, and it's good to maximise seat time while we can. -
Get serious with current chassis or upgrade to something newer?
Dale FZ1 replied to robbo_rb180's topic in Motorsport
This is the first and best thing to invest in. 100% agreed -
Get serious with current chassis or upgrade to something newer?
Dale FZ1 replied to robbo_rb180's topic in Motorsport
Most honest comment would be you need to consider what you want to achieve in motorsport. Big difference between just having a run, and getting in there wanting P1. By your report, there was a big time difference between you and Paul Morris around Reid Park. Do you really want to beat him and others? Talent, current seat time, car spec all part of the mix - as we'd all appreciate. High spec car is going to cost proper $$ and effort if you want one built with cage, suspension, brakes, wiring, gearbox and diff. (Deliberately not talking about engines). And if you want aero, that's part of the initial build/spec planning. Chassis - there's a reason Toyota 86 is popular. Look at a bare shell and they are a substantial improvement over an S13. As you would hope/expect. Cage - you'd expect between $4-6k as a start, depending on how extensively you want things done (talking at good clubman spec here). Perhaps best to look at regs of classes and events you'd like to compete in, and build to that (regardless of whether you stay with S chassis or move on). Turn key options are attractive, even if it entails making running improvements along the way. My suggestions would be to at least consider an 86 Cup car, a Clubman, a MARC, and a TA2. Repairs/re-engineering the S13 is also still a reasonably sound approach. SEQ is a good 14+ hours run south for you, but there are a number of competent fabricators and engineers with experience to make one work well. I've got a couple of ideas who may be useful, will send PM on details. -
@mlr that's an expensive donor chassis. Nothing special about an E30 except light weight, and compact dimensions. Body lacks rigidity. Rear semi trailing arm suspension very similar in concept and execution to a Datsun 180B. And the 80s spec M20 donk is even less exciting than a RB20E, plus more expensive to overhaul. If Dose gets any urge to look at that, I will send him a pair of knitting needles. The pain of those jabbed in the eyes will take his attention away from the BMW.
-
@Wheezy depending on who manufactured your turbo, there may well have been impeller options. With Kinugawa there certainly was. From recall, I selected the "middle spec" turbine which was 11 blade (stock being 12, and 9 being the highest flowing + lightest), and "standard" 6+6 compressor. There was also a full 12 blade billet comp impeller option for high boost applications. Thrust bearing was about 270 degrees for all units. With all of that, I ran the 11 blade turbine, 12cm housing, standard 12 blade comp, and the compact comp cover. Main target was decent turbine flow efficiency, and a modest power requirement under 400rwhp. It performed the required task, reliably. And there was room for much more. Boost response was satisfactory, not "awesome". At the price point there was little to complain about. I reckon yours will be a good thing, interested to see whether it can run to your power target. What I really like is your choice of Emtron and some decent sensors. Suggest you ditch that OEM CAS. I found greatly reduced timing scatter with a NZ Wiring sensor kit, if that's any help.
-
Got anymore detail on that turbo? What spec impellers and turbine housing? I ran a Kinugawa one with 11 blade turbine, 12cm T3 single scroll for several seasons. Was very good performer at the price point, only mistake I made was to spec a more compact comp housing with 3 inch inlet. My car was intentionally kept at modest boost and 375rwhp for track, but a short dyno test with more boost showed 460rwhp on 98 petrol was no problem. The bigger comp cover would have been a better choice if I wanted/needed to pursue bigger hp than that.
-
Looking great Neil. You'll be feeling like the king. Plans for a hoist of some sort too? My shed got a couple of strategically placed windows for natural lighting to make life easier when doing certain jobs. Bring on more pics and story on the setup.
-
RB25DET turbocharger "stock" a/r.63 or "oversized" .70?
Dale FZ1 replied to JC71's topic in Forced Induction Performance
The location of manufacture is not the issue. But the spec of the unit (dimensions, bearings, quality of castings and machining) is. I've run a Kinugawa on RB, generally it was fit for purpose especially at the price point. -
RB20 Turbo selection (twinscroll housing advice)
Dale FZ1 replied to iruvyouskyrine's topic in Forced Induction Performance
Changed back to OEM for appearance, or performance? Not sure what ruined your car- 154 replies
-
- rb20
- twinscroll
-
(and 3 more)
Tagged with:
-
RB25DET turbocharger "stock" a/r.63 or "oversized" .70?
Dale FZ1 replied to JC71's topic in Forced Induction Performance
Both of those units are a long way from a stock bolt in option and would probably perform well below expectations compared to the OEM turbo especially without ECU tune changes. OP - 0.7A/R comp housing does not provide any basis for comparison of 0.63 turbine housing on the other unit. There's some very good resources out there in internet land if you want to get your head around turbos. There are some decent replacement turbos out there that will bolt in and do the job you want. Try an experienced supplier like Hypergear and see what can be done cost effectively. -
I generally find there's too much going on to have time looking at a lap timer. Cool tech though.